Custom Packaging for Evolving Market Needs: Adapting to Change
Why Packaging Design Changes Are Important for Brands
Packaging changes are essential for brands to stay competitive, improve sales, stay up-to-date with customer preferences, and maintain strong brand identity in a highly competitive market. If you stay up-to-date with packaging design, you already know that it's not uncommon (and certainly isn't wrong) for brands to focus on a logo or packaging redesign every so often.
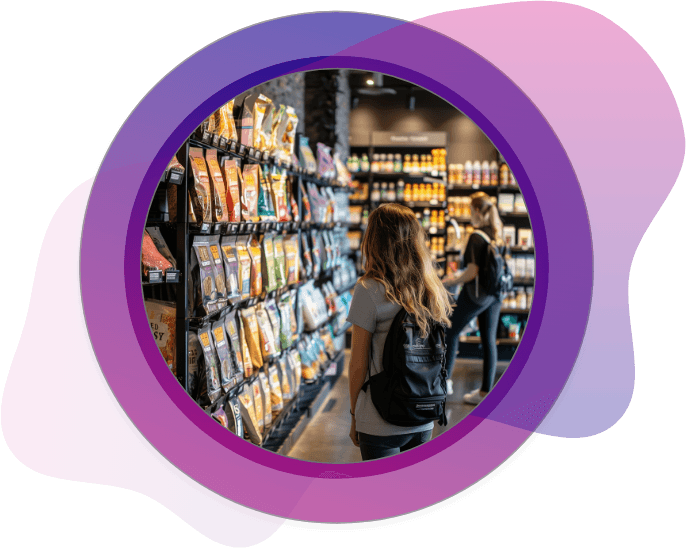
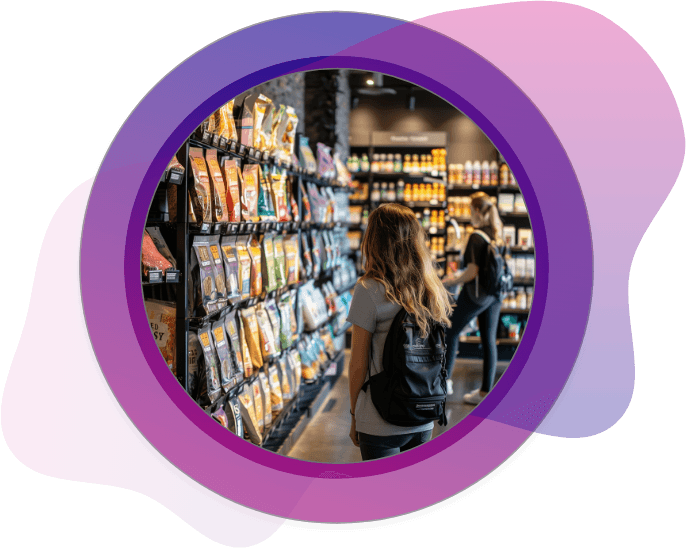
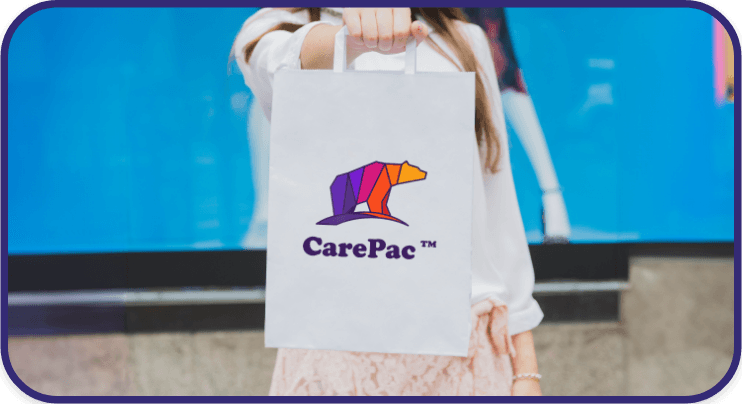
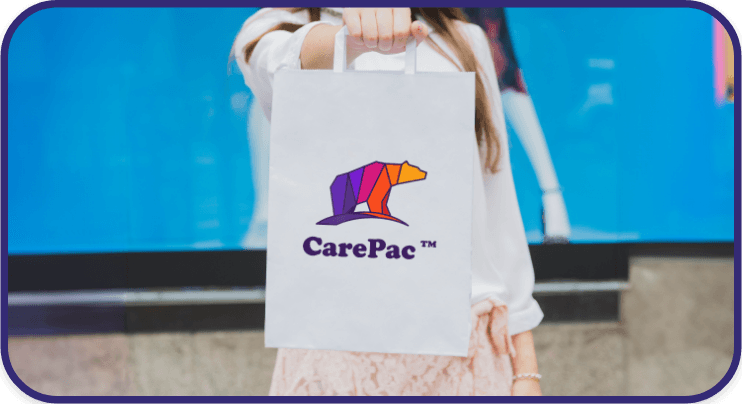
Whether it's adjusting the product name, testing a different logo or label look, enhancing the visual appeal, improving usability, or changing the material so it's more eco-friendly, there are several ways brands can move past their original packaging and create product packaging that feels fresh in this modern world.
In this blog, we'll discuss old packaging vs new packaging and how you can enhance your brand image by testing a new design.
Old Packaging vs New Packaging: Key Drivers of Change
Sustainability and Eco-Friendly Packaging Redesign
With growing environmental awareness, consumers increasingly seek eco-friendly packaging options, requiring brands to adopt sustainable materials and practices. If your loyal customers are looking for brands they support to make positive changes relating to the environment, giving your packaging design a fresh look by shifting from difficult-to-recycle plastics to materials that can be composted might be a great next step.
Gather feedback from your consumers, see what's important to them, and consider incorporating those elements into the redesign process. This is just one example of how you can use valuable customer feedback to sell more.
Staying Current with Your Competition
Many brands go through a packaging redesign so they can stay current with the market. One thing you can do is walk through the aisles at your local market and see what your competitors are doing with their packaging. Pick it up from the shelf and actually hold it in your hands. How does it feel? Look? Smell? Bonus points if you buy it and take it home from you to see how it opens. Take your own surveys and do your own research to see what benefits other brands are getting from their packaging. File away what you learn and incorporate it into your design later.
Technology and Smart Packaging Innovations
Yes, improving sustainability is important, but so is bringing your packaging to the 21st century during the packaging redesign process. Some key innovations to consider include NFC-enabled packaging, QR codes that can help enhance transparency and give you another way to engage with your target audience, using biodegradable materials, or using active packaging for extended shelf life. An example of "active" product packaging includes using theses like antimicrobial coatings or oxygen scavengers.
Policy & Regulatory Changes Impacting Your Original Packaging
Another key driving factor of ditching old packaging in favor of new packaging is regulatory or policy changes. From bans on single-use product packaging, especially if it's made from plastic, to the cannabis industry evolving what needs to be included on the packaging itself, if there's new regulations that focus on product packaging in your specific industry, it might be time for a new packaging design.
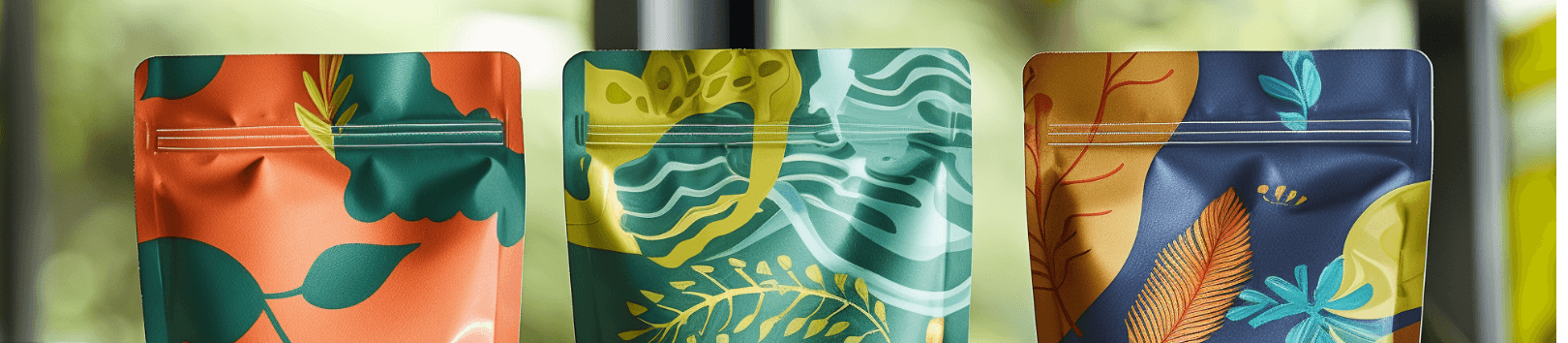
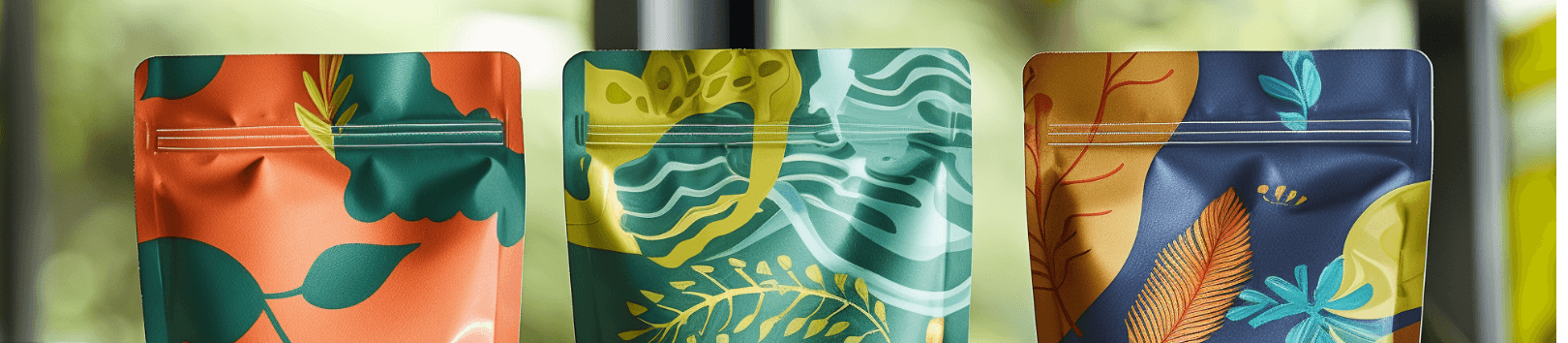
What Consumers Expect from Modern Packaging
There are several things consumers expect from modern packaging design. If you're currently redesigning packaging for your band, here are some things to consider:
Personalization and Custom Branding
Customer feedback shows that they value personalization and custom branding because it makes them feel special and valued. If you send a customer cards or boxes with their name on it, it makes them feel like you went the extra mile and could encourage them to purchase from you again in the future. You want to do whatever you can to get a repeat purchase from your consumers.
Create Convenience and Functionality
Ultimately, the new design you're testing should be functional and easy to open. Don't you hate it when you break a nail trying to open a box from a retail store? Listen to the concerns of your customers and, if this is one of them, your packaging redesign should focus on making your packaging easier to open than your competitors. This is one area where testing your packaging with a control group can be helpful. They'll let you know what you're doing wrong and how you can further enhance your image.
Packaging that Reflects your Brand Identity and Values
Consumers, especially younger ones, care a lot about your brand story and if it's something they can relate to. If your co-founder is especially philanthropic or from a disenfranchised community, you might want to include their story on your package. Make your packaging personal and use it as an opportunity to showcase what makes you more appealing or different from other retailers. Consumers want to buy from brands they find similarities with.
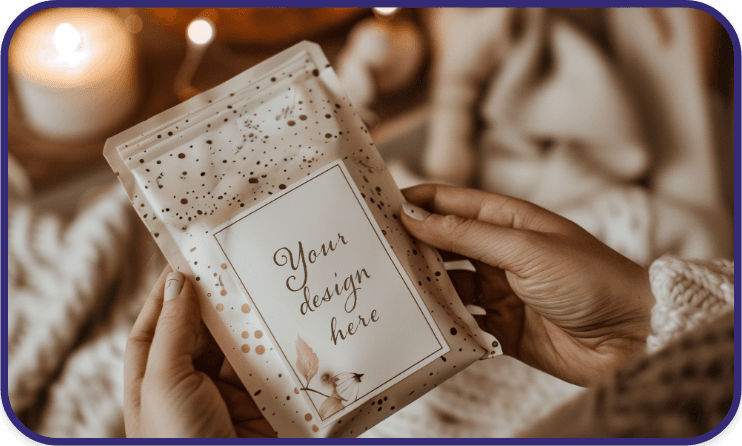
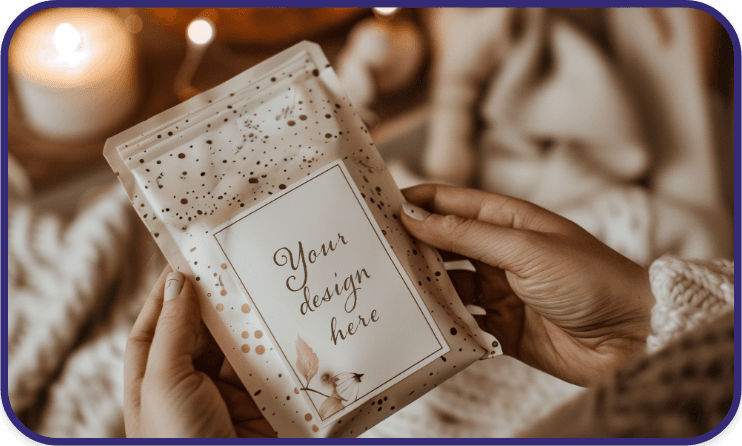
How Brands Can Adapt to Evolving Industry Trends
One important part of adapting to evolving industry trends is to get ahead of the redesign before your sales suffer. Instead of thinking "what can I gain from a packaging redesign?" ask yourself what you can lose out on from not doing it. Your packaging redesign should be proactive, not reactive. It should give your product new life on the shelf and look current without detracting from the look of your brand.
It's important to maintain the fidelity of your brand throughout the redesign process. This is one area where getting input from those outside of your company can be helpful. Ask friends, family, or even strangers what they think about the redesign.
CarePac: Your Partner in New Packaging Design
CarePac is a trusted partner that helps brands and consumers navigate these changes, offering custom packaging solutions tailored to their needs. One example of our many differentiating factors is that we actually consult businesses on material choices, design or concept updates, and compliance, ensuring a seamless transition to better, future-proof packaging. Get out of the past and create new and improved packaging that'll help your product sell.
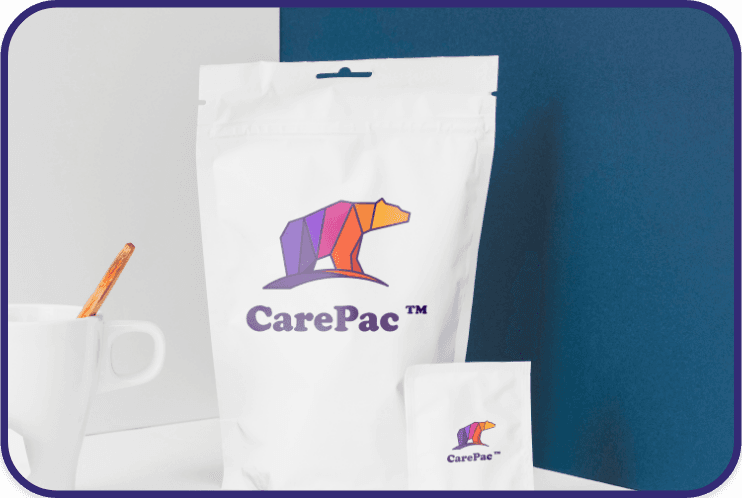
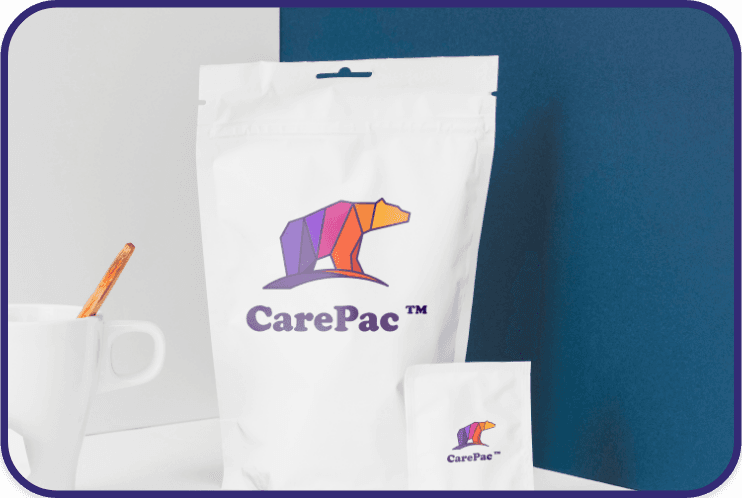
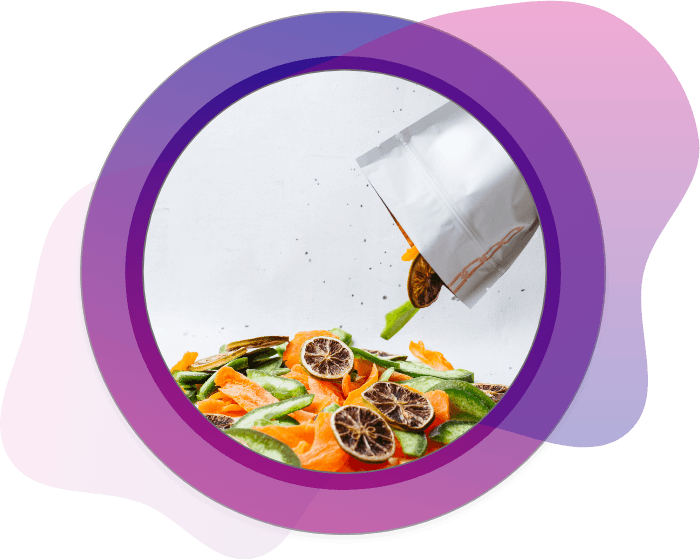
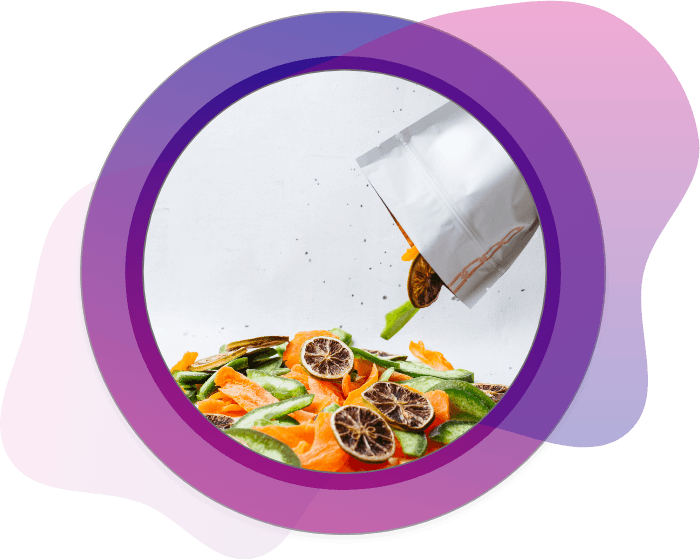
The packaging landscape is constantly evolving—brands must stay ahead by embracing sustainability, smart technologies, and regulatory shifts. CarePac is here to make that transition effortless, and we will help you create and design packaging that remains competitive, compliant, and consumer-friendly. Ready to elevate your packaging? Contact CarePac today for expert guidance on your next redesign!
Have questions about your existing design, including your logo or label placement? Connect with us for a design consultation!
Let's Get Started
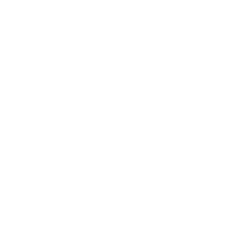
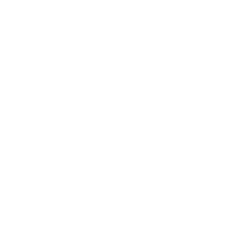
Made In
The USA
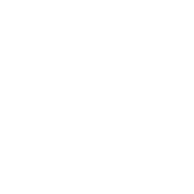
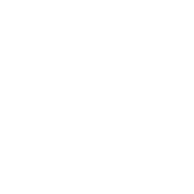
Full Pouch
Customization
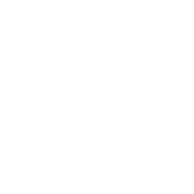
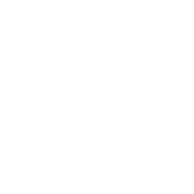