Packaging Polymers
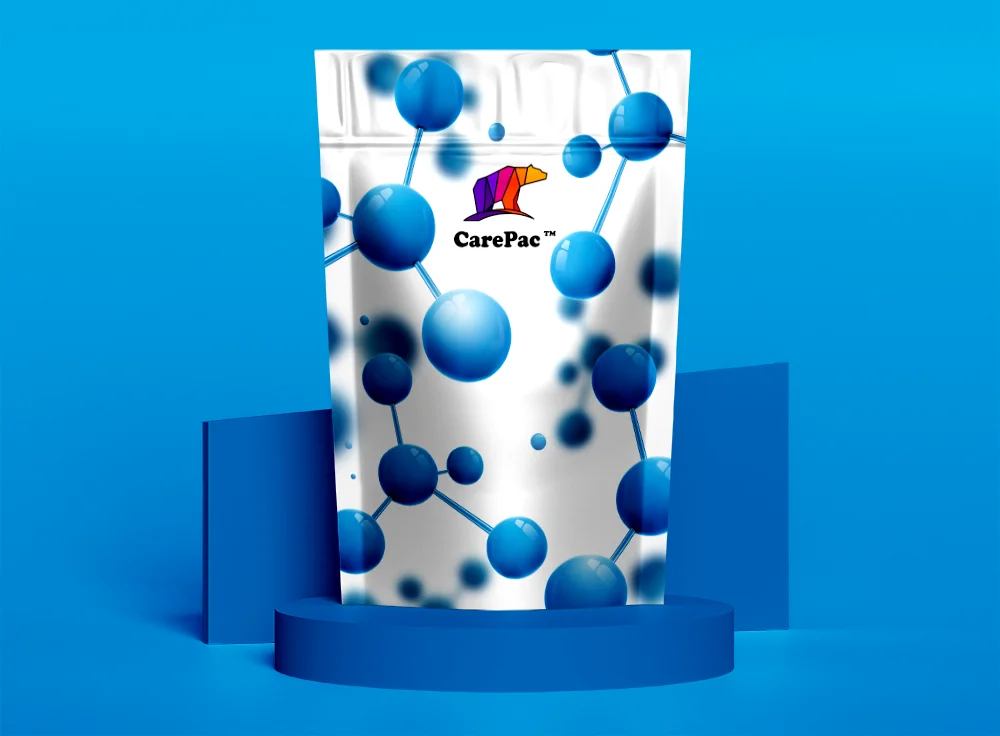
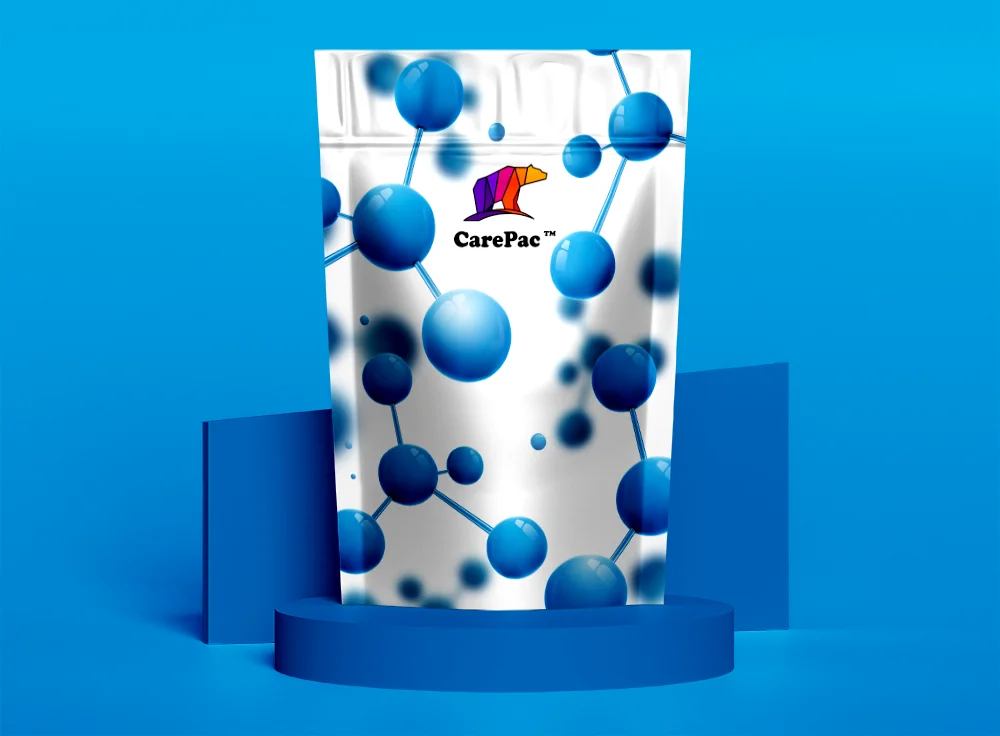
The term 'polymer' is used to refer to an industrial substance or other materials consisting of very large molecules, called macromolecules. Polymer packaging can be synthetic or natural in origin and can be rigid or flexible in nature. Examples of these molecules in nature include proteins, starches, and cellulose. Synthetic polymers often used by consumers in carry bags and other products include nylon, high density polyethylene, durable rubbers and more.
Here, we'll discuss the different types of industrial polymer packaging materials that can be used in flexible packaging solutions, their critical benefits, any known risk, and their composition.
What Are Polymer Packaging Materials?
One of the largest industrial applications of plastic polymer packaging is as flexible packaging solutions and materials (35% of polymers are estimated to be used for packaging). Packaging items using polymers have many benefits, including increasing the life of your products on shelves, lower cost, and lighter weight and more attractive than other packaging options like glass bottles. Polymer packaging, especially laminated packaging, is a core type of food packaging, as it is attractive, functional, efficient, improves the shelf life of your products, and has cost effectiveness properties.
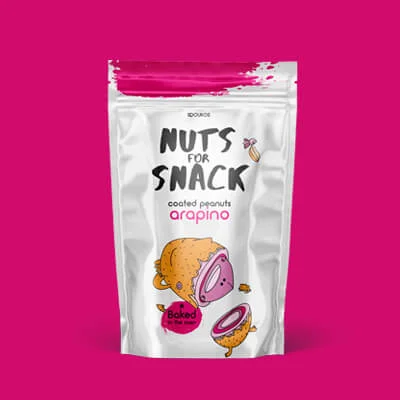
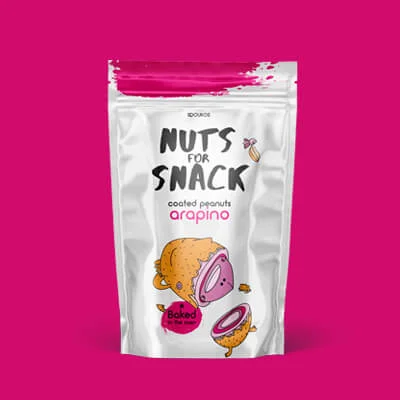
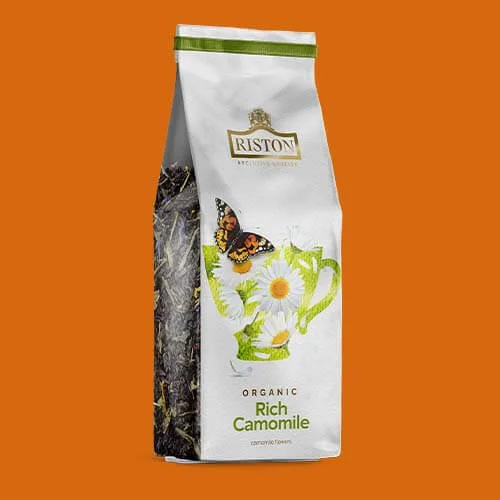
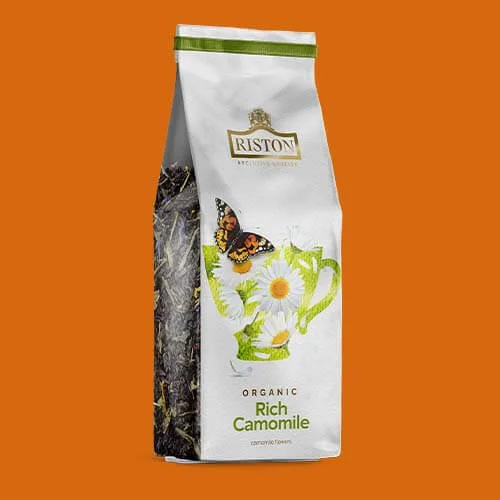
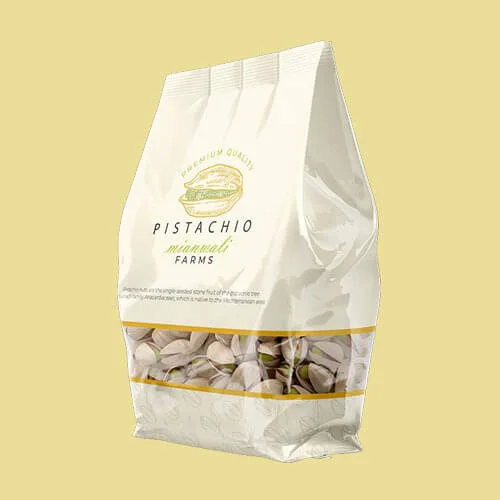
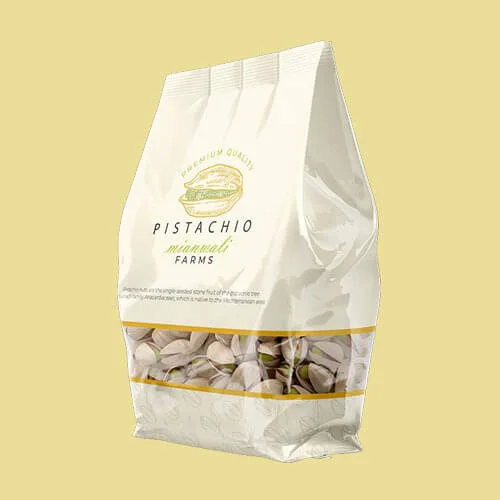
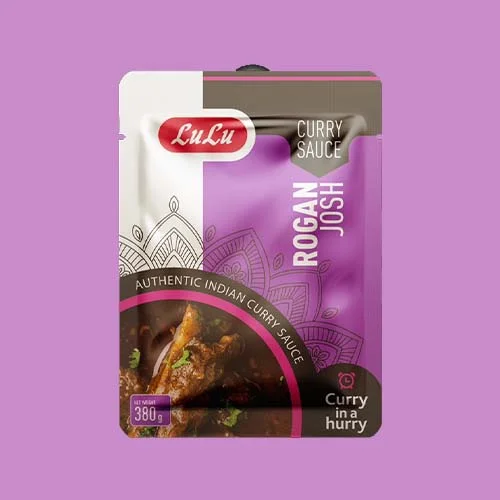
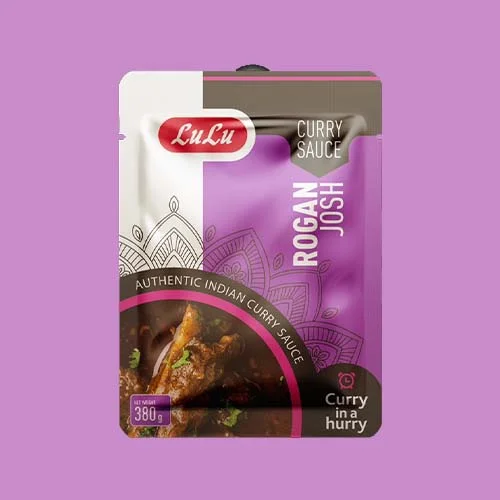
Flexible packaging solutions for foods include a range of different durable materials. Polymeric materials by the percentage of packaging include PET, high density polyethylene terephthalate 9%, polypropylene (PP) at 11%, polystyrene (PS) 11%, with other polyolefin plastics including polyvinyl chloride (PVC). These can help increase shelf life, preserve freshness, and is a great flexible packaging option for many applications.
Next, we'll discuss the different materials that are classified by the American Chemistry Council as polymer packaging, including polyethylene and polyethylene derived plastics.
Polyethyleneabbreviation | Name | Densityg/cm3 | CommonApplication |
---|---|---|---|
HMWHDPE | Ultra high density | 0.93 | Plastic parts |
HDPE | High density | >0.941 | Bottles |
MDPE | Medium denisty | 0.92 - 0.94 | Closures, and clamshells |
LDPE | Low density | 0.91 - 0.94 | Pouches and bags |
LLDPE | Linear low density | 0.915 - 0.925 | Pouch sealant layers |
VLDPE | Very low density | 0.88 - 0.915 | Pouch sealant layers |
PVC, minor plastics & their applications
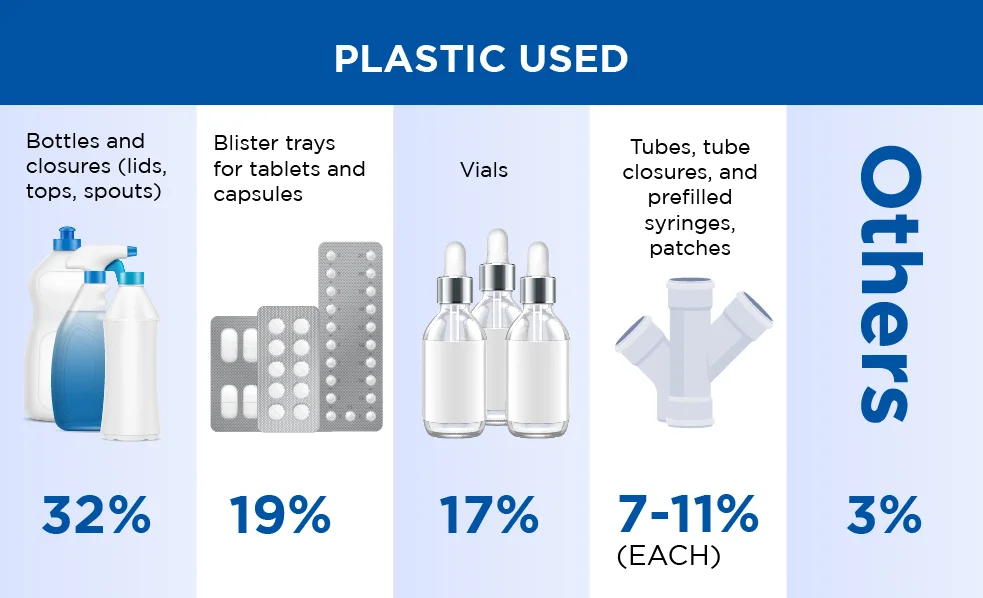
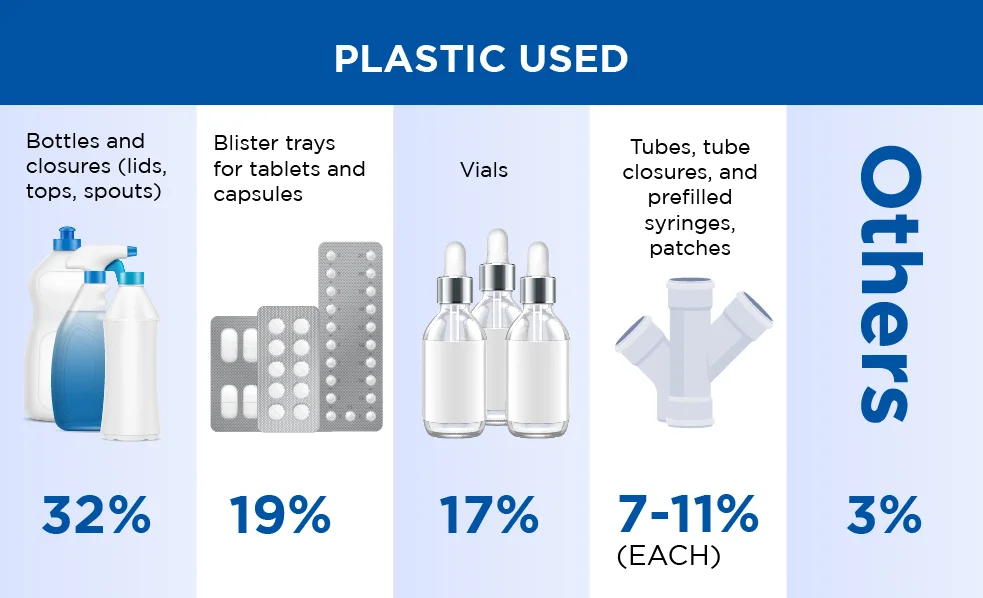
PVC, which is notoriously difficult to recycle when compared to others on this list, typically winds up in landfills, and is the subject of numerous environmental concerns over the evolved toxic compound, vinyl chloride monomer (VCM), which constitutes only about 5% of plastics. Other minor plastics, for example, acrylonitrile-butadiene-styrene (ABS), polytetrafluorethylene (PTFE), and nylon, constitute only about 3% of usage together.
Bottles and closures (lids, tops, spouts) account for 32% of all plastics used, followed closely by blister trays for tablets and capsules at 19% and vials, which also constitute quite a high proportion at 17%. Tubes, tube closures, and prefilled syringes, as well as patches, account for between 7% and 11% each. All other applications of plastics for packaging constitute about 3% of materials.
Biodegradable plastics
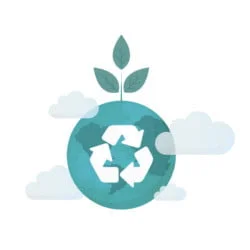
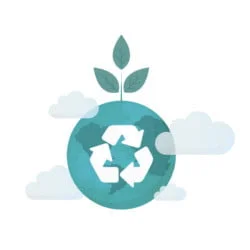
Biodegradable plastics are a series of different materials of contemporary interest and include composites of starch or other biomaterials with or without the presence of more environmentally persistent and traditional polyolefin plastics. Examples include poly-caprolactone (PCL), polylactic acid (PLA), polybutylenesuccinate, polylactic-co-glycolic acid (PLGA), nitrocellulose (NC), cellulose acetate (CA), methyl cellulose, polyesteramide, and polyamide (PA).
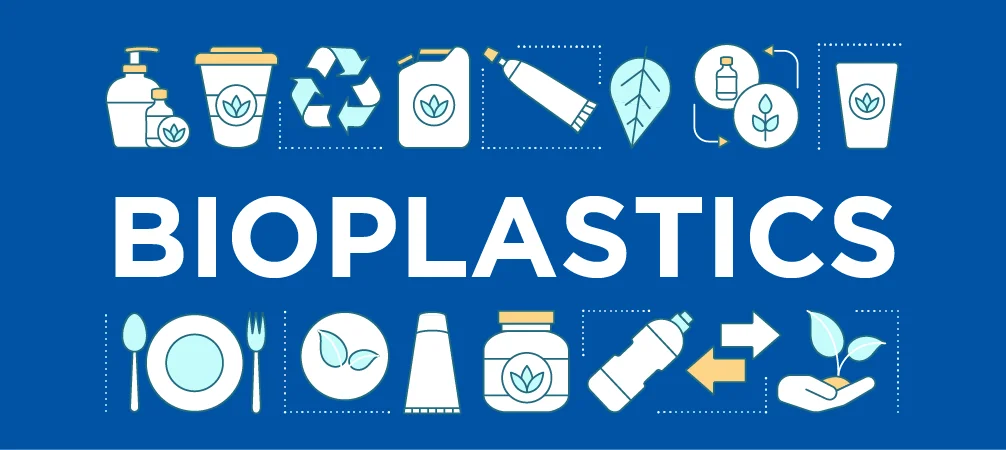
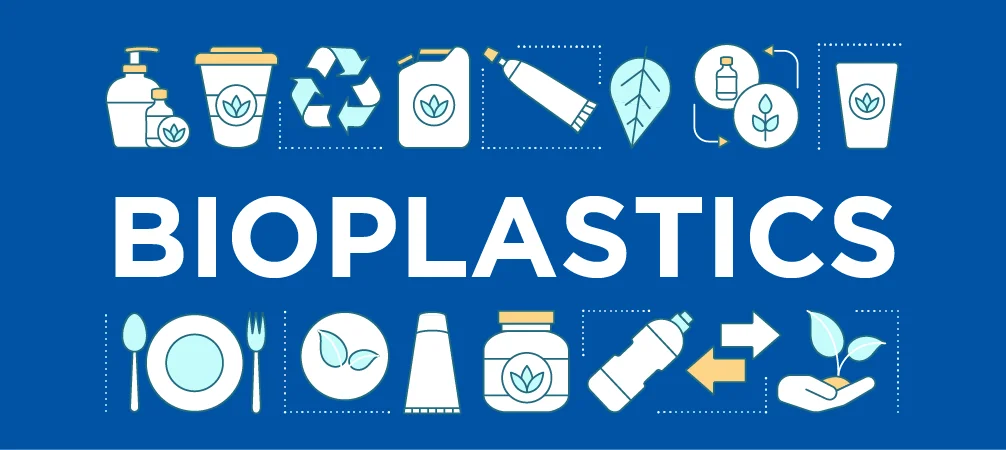
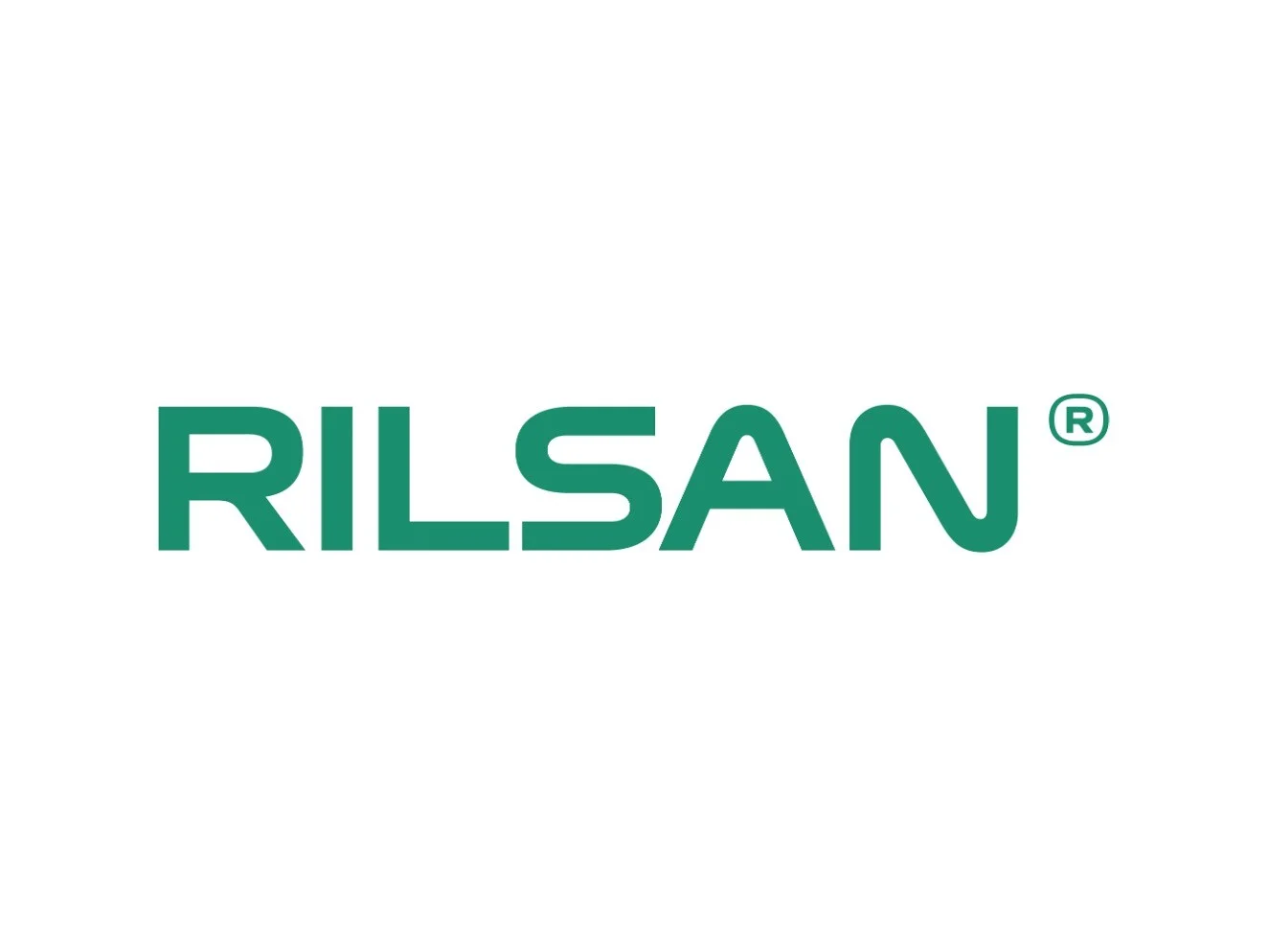
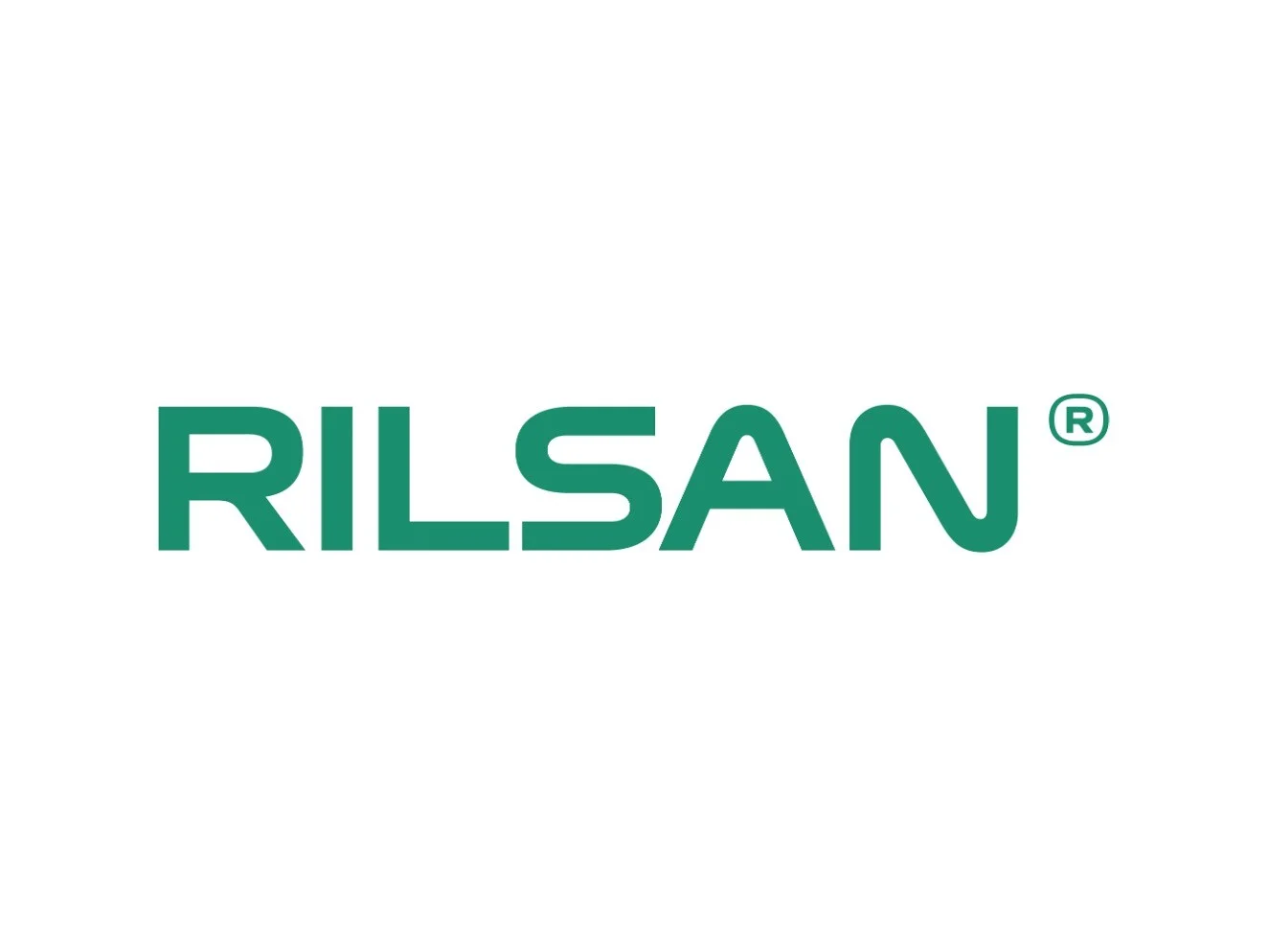
Rilsan® is a bioplastic produced from castor beans by Arkema (France), and is among one of the most popular flexible packaging solutions. Polyhydroxyalcanoic acid, polyhydroxybutyrate-co-valerate, poly-B-hydroxybutyrate (PHB), starch-PLA, starch-PCL, and starch-Ecoflex, where this last compound is an aliphatic aromatic polyester (polybutylene adipate-co-terephthalate [PBAT]), and others such as polybutylene succinate terephthalate are new products
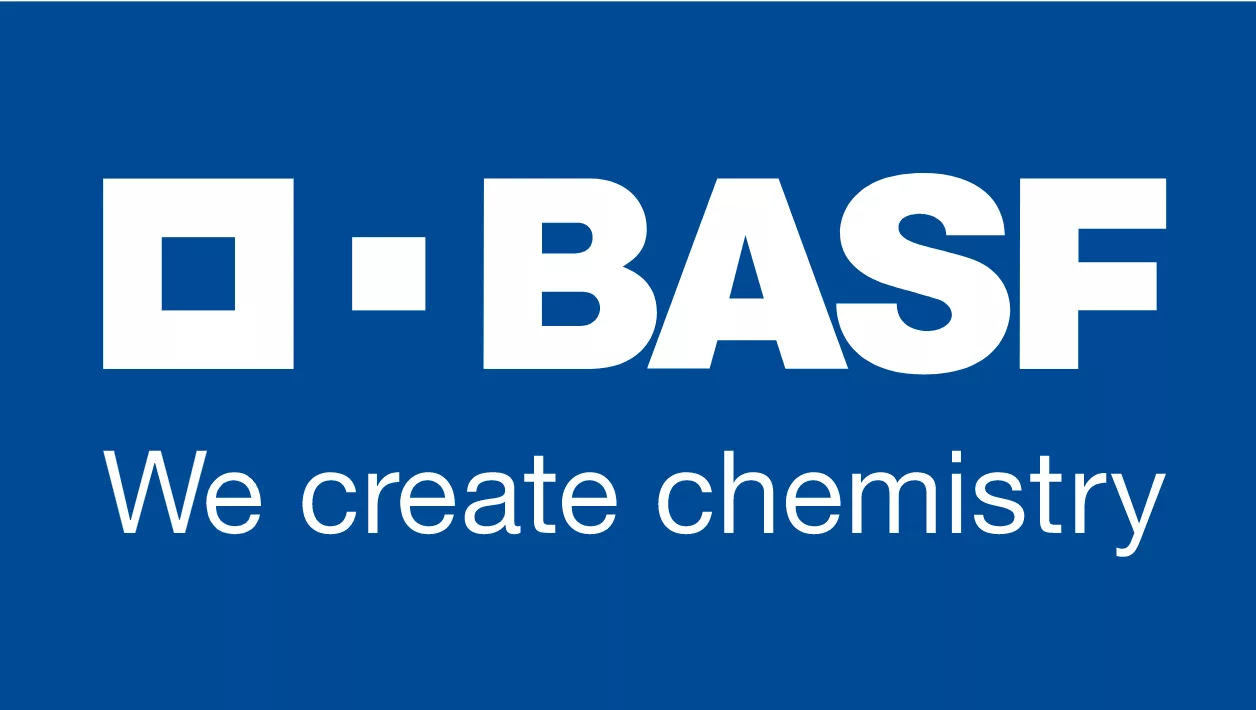
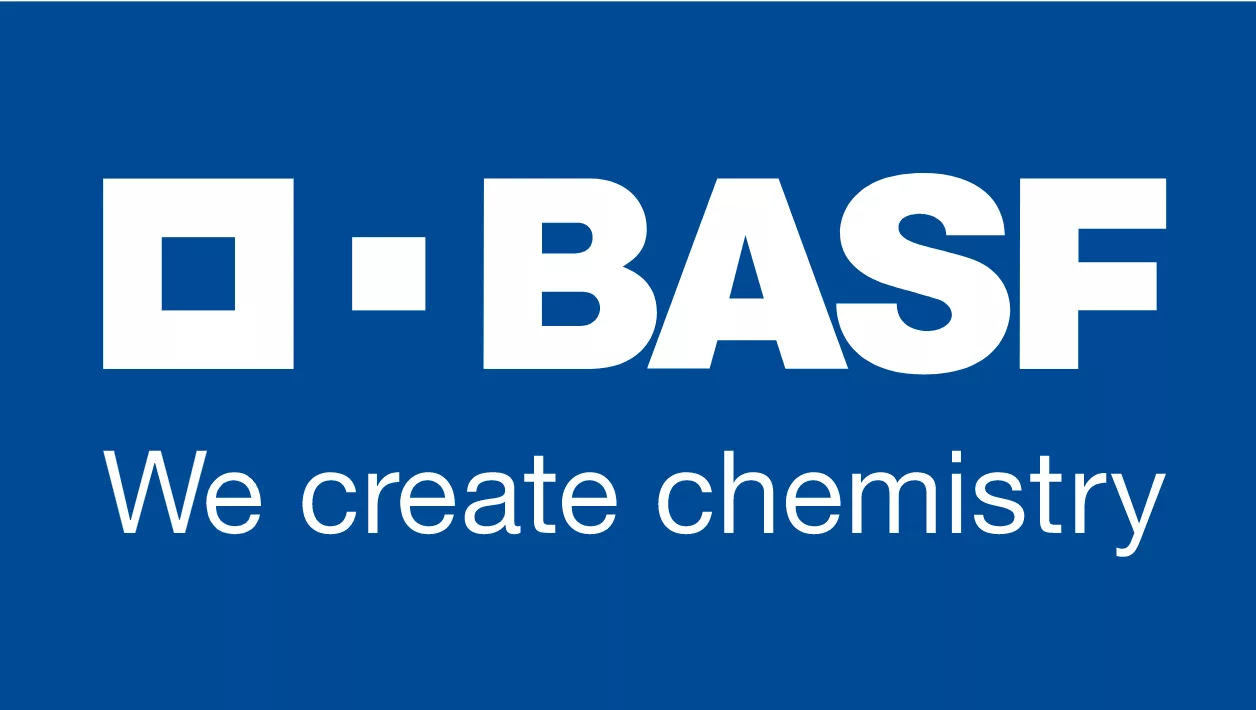
PBAT is production was pioneered by BASF. Glycerol (10-20%)-plasticized chitosan (maize), zein (soybean), protein-keratin (rapeseed meal), protein (wheat gluten)-based water-containing (10-20% plastics, ethylene bioplastics, and those making use of nano-technology such as silicates represent a new array of bioplastics. Hemp oil, soya and other vegetable oils, vegetable starch, and sugarcane give a composite 'bioplastic' (Toyota Motor Corporation); PLA and 20% kenaf (hemp) fibre (NEC Corp.) also represent new media.
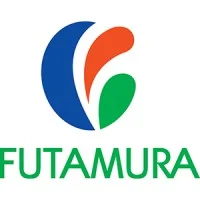
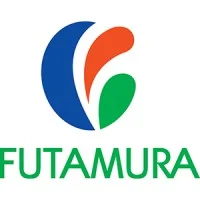
NatureFlex is a cellulose film produced by Futamura. It is available in several configurations including a vapor metalized form which is more resistant to mositure and oxygen migration and other contaminants which allows for increased shelf life for food packaging, and has been used in various applications including candy packaging, and other consumer goods that require better barrier.
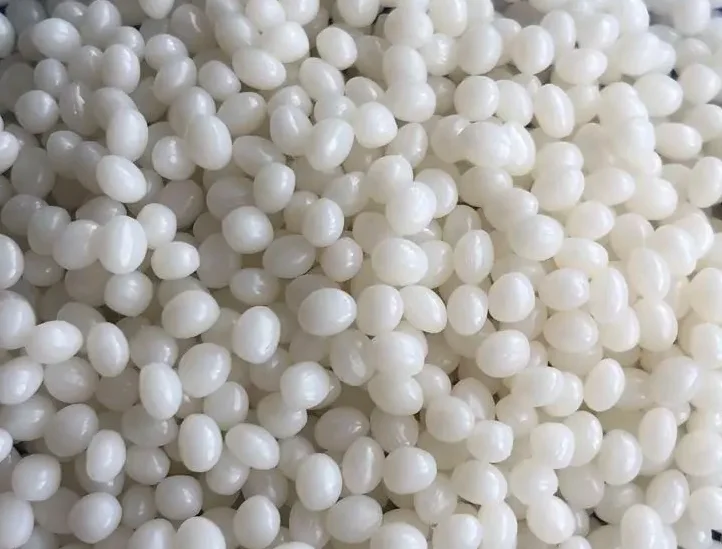
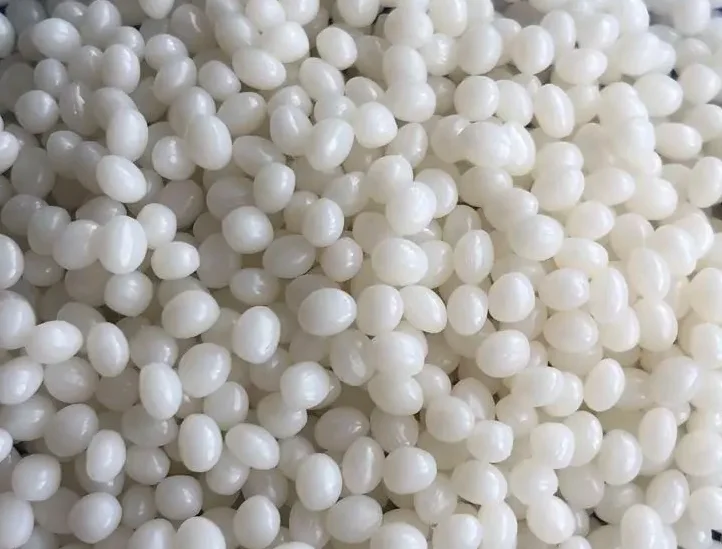
PBS (Polybutylene succinate) is a sealant layer solution which allows or ambient compostability. PBS has can be efficiently laminated to NKME metalized NatureFlex, and is a food contact grade sealant layer.
The use of these bioplastics in medical use applications and their overall durability as compared to traditional plastics is a matter of continued exploration, and study by various companies.
Starch
Starch is relatively inexpensive, adaptable, and a hugely abundant resource generated from cereal and vegetable processing. Materials such as Mater-Bi from Novamont have poor gas and water exclusion (10 000-100 000 times poorer than most polyolefins), low melting points (60-120 °C), and low mechanical strength, such as tensile strength (15-50 MPa), compared with conventional plastics, which melt at 160-240 °C and have tensile strength values of 20-80 MPa.
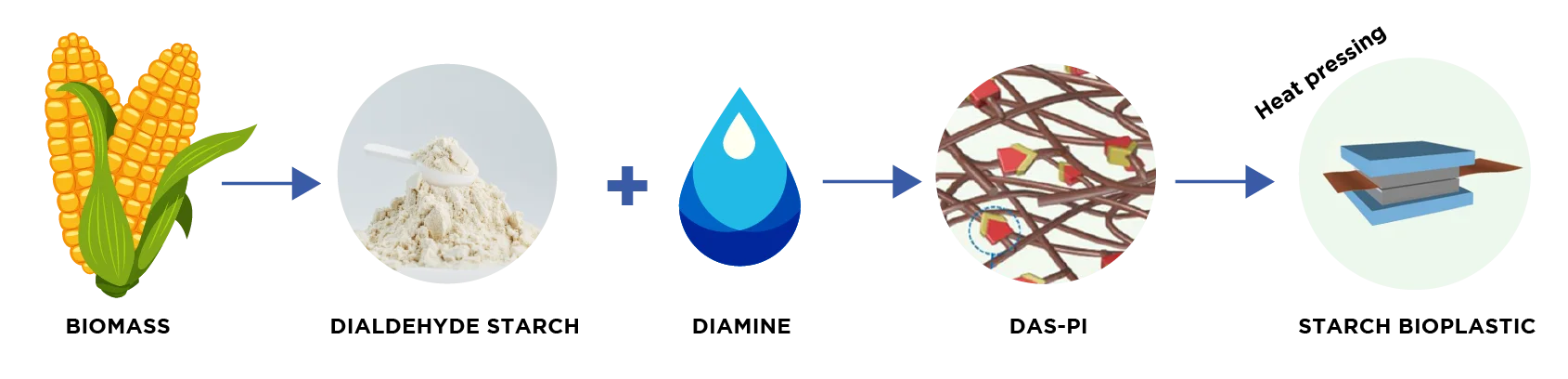
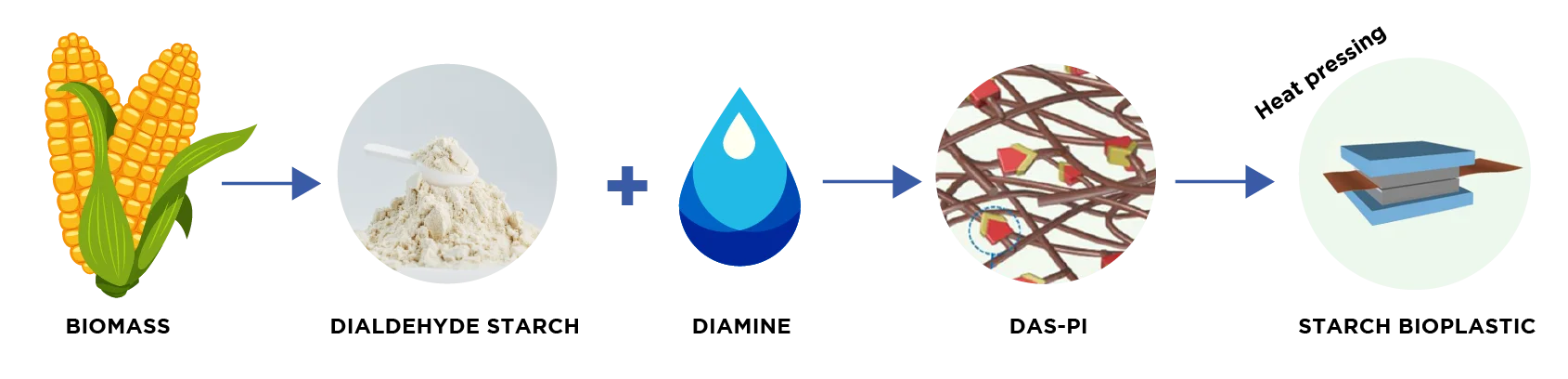
These deficiencies mean thermoplastic starch-based biomaterials (for thermosetting applications such as trays) may be combined with more biodegradable contemporary plastics such as ethylene vinyl acetate (EVA) or ethylene vinyl alcohol (EVOH) because of the benefits of their gas and water vapor barrier properties, which may be 1.2-2.4 times poorer than PP, which is one of the better barrier materials.
Experimental plastics
Conventional synthetic plastics are highly favored in terms of their physical properties but increasingly less so, based on environmental impact post initial use. Consequently, a range of experimental and novel bioplastics are constantly being developed to alleviate environmental injury and accumulation in the ocean systems and the food chain.
Past innovations with limited success have included milk protein bioplastic fabricated using the milk protein casein in the presence of 4-5% formaldehyde as a cross-linking agent, the inclusion of TO, as a filler, and 1% clarifying agent such as ethylbenzene aniline or trixylyl phosphate. Zein, a maize protein cross-linked by formaldehyde developed in the past, continues to be of interest since maize growth can be considered to be a sustainable crop. Other less enthusiastically received plastics have included a soya, castor bean, and animal blood-based plastic that, apart from a dark color, was always likely to meet with some societal resistance and thus fail.
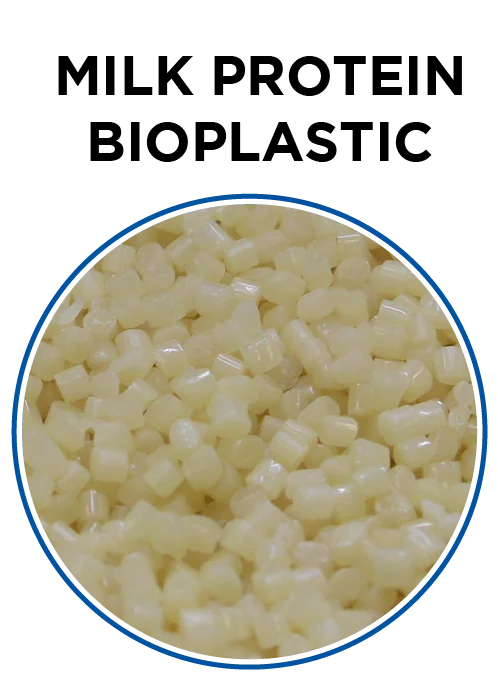
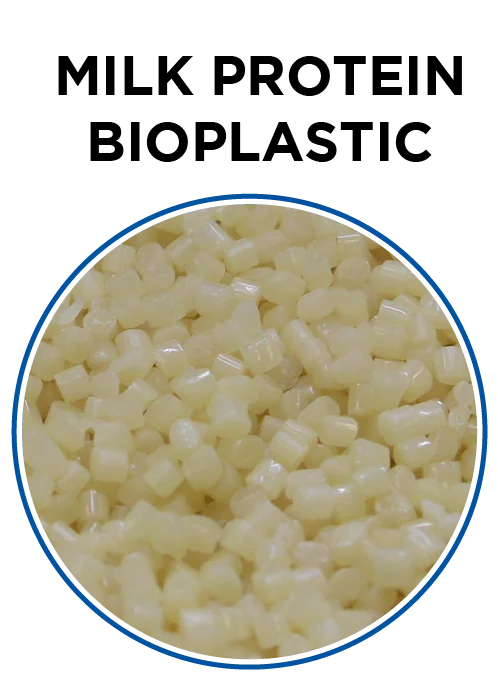
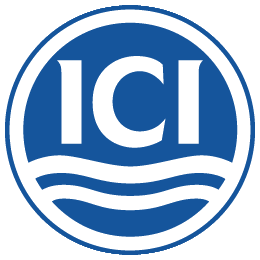
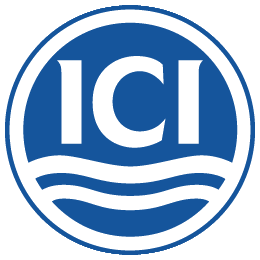
Imperial Chemical Industries (ICI) developed Ardil fibre, which was used some time in the last century (around 1940) and was generated from spun and bonded groundnut proteins. In more recent times, the substance 'gutta percha', obtained from the Palaquium oblongifolium leaf, has gained interest for commercial use since it represents a natural form of rubber latex based on trans-1,4-polyisoprene that can be vulcanized with sulfur and molded/cast to a desired form. Other natural materials have included shellac, an exudate of aldehydes and hydroxy acids of lactides and esters of waxes from the female lac insect from Southeast Asia.
Fabricated films
Fabricated films for various purposes can be used directly or as part of multi-layered composites known as laminate films. Industrial over-wrap films often use single materials such as PP or laminate films. The over-wrap is made from blown and cut films of a range of plastics such as PVdC, PP, and HDPE, which are often heat-seal bonded to a tray or bottle.
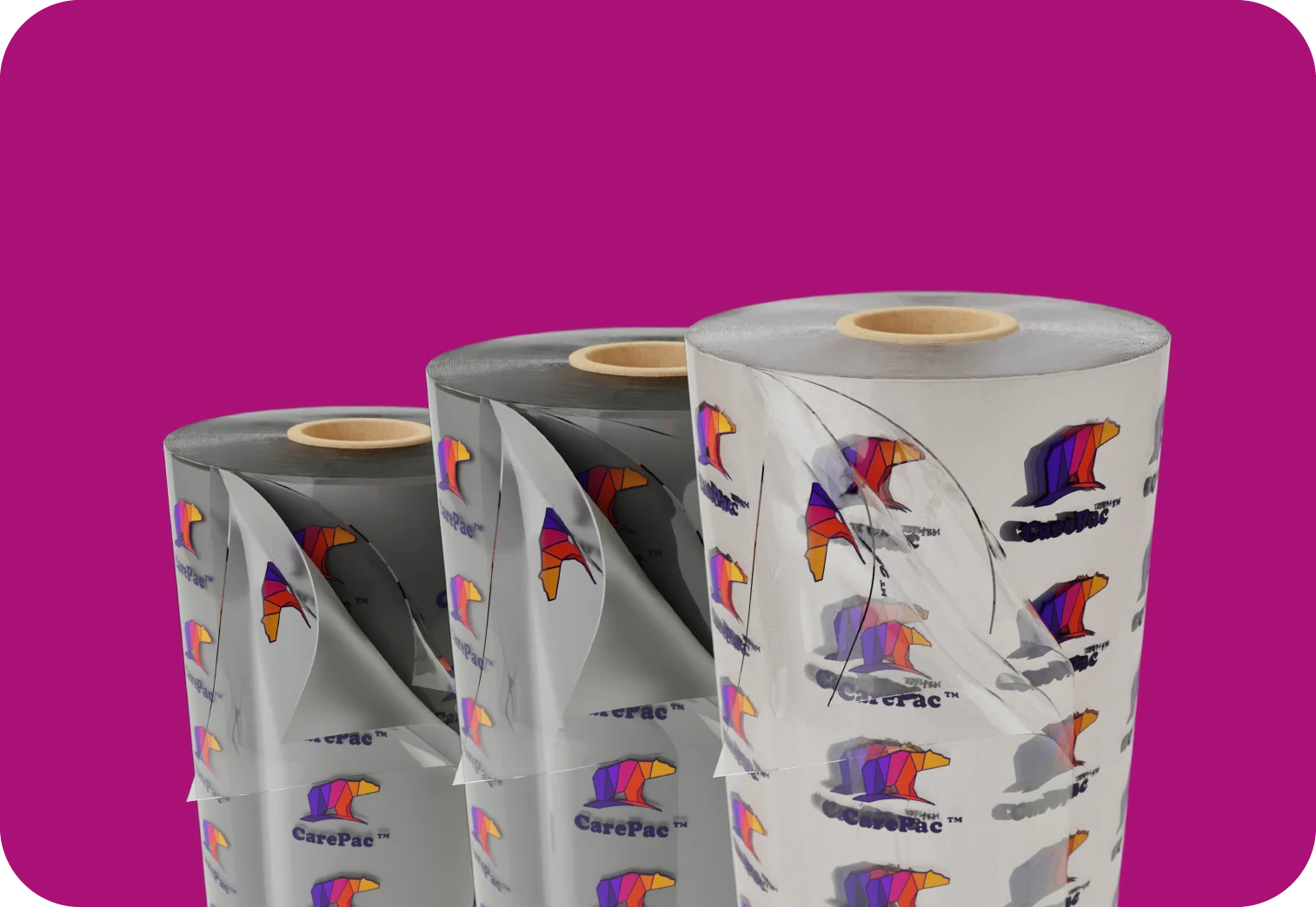
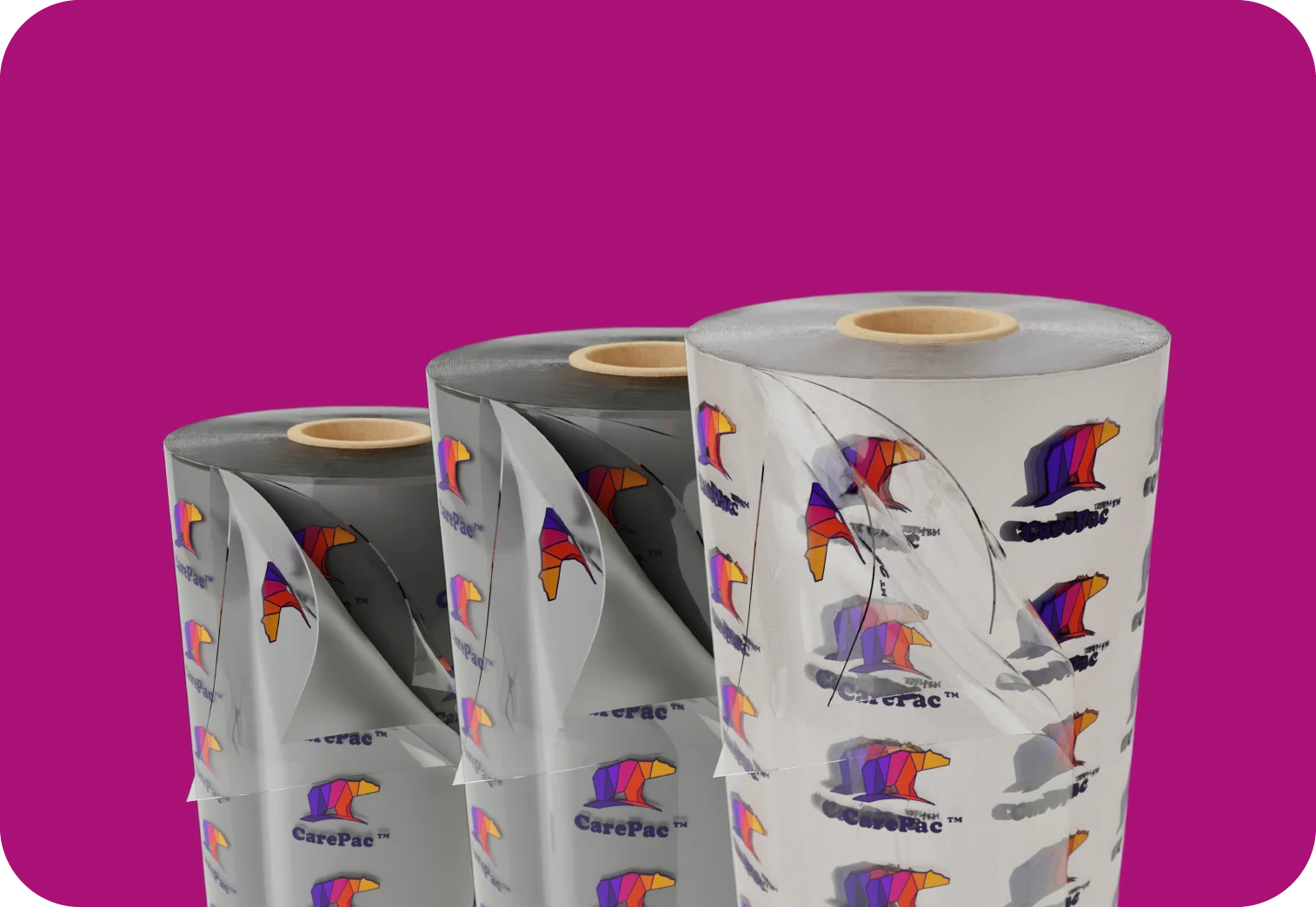
Fabricated films vary considerably in the sheet thickness obtained in standard production processes. The thickness of sheeting can be modified but the thinner films obtained are HDPE (~12 m), PP (~14-30 m), and PVC (~18 m). Thicker standard films are produced from LDPE (~20-25 pm; referred to as 100 gauge), LDPE-co-PVA heteropolymer (~20 m), cellulose film (~20 um), and coextruded film with multiple layers (~30 um).
LDPE
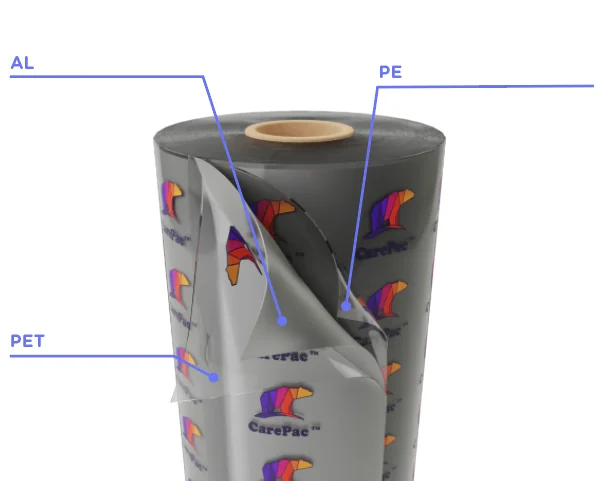
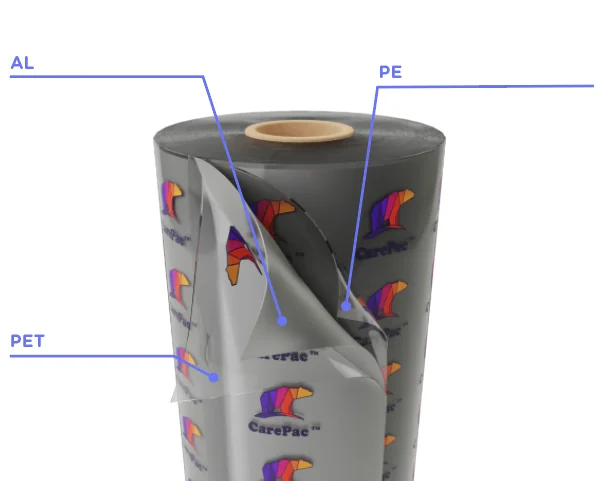
LDPE is also made in a range of sheet thicknesses that can vary from 20 to 150 pm. Films can be plasma treated and metalized to provide light reflectance, or in some cases, plastic film can be bonded to thin aluminum foil and paperboard. Pharmaceutical blister packs often make use of webbing film of a thicker form that can be fabricated from up to four layers of material bonded by an adhesive. In order to ensure uniform welding or heat-seal formation the glass transition and melting point characteristics of film materials need tight control.
Cellophane
Cellophane is a convenient industrial biodegradable film used for plastic packaging that has fairly good moisture barrier properties. The polyethylene polymer is also known as regenerated cellulose or viscose and is also used for fabrics just as it is used as a packaging material. The material is formed when substrate is dispersed in an alkaline medium (NaOH) and then mixed with carbon disulfide (CS2) which is a fairly dirty process, and is considered toxic to workers. Alternative processes exist that do not require carbon disulfide, such as the lyocell process.
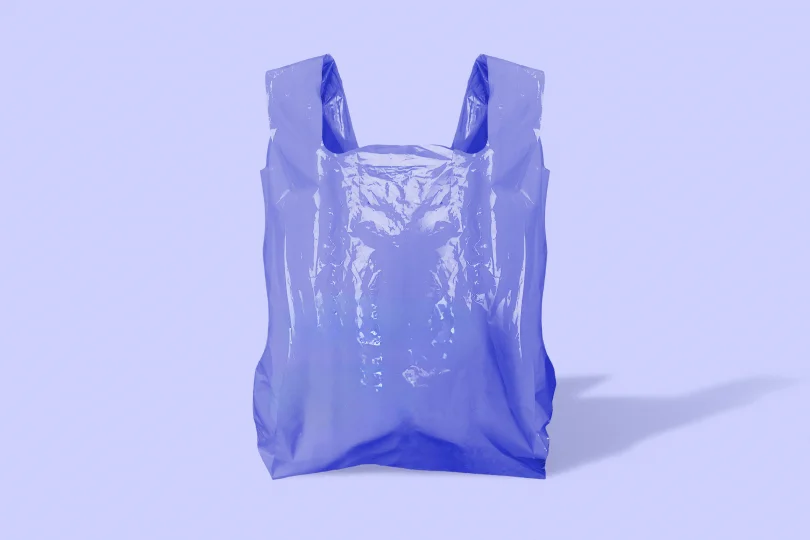
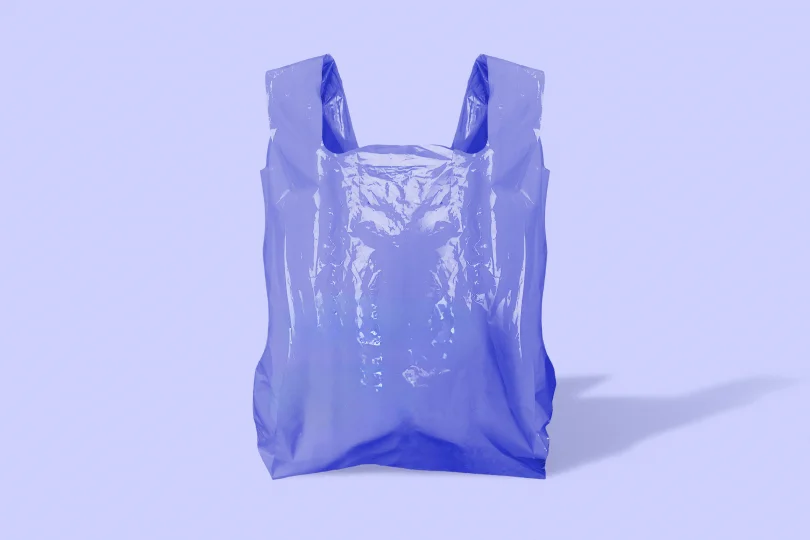
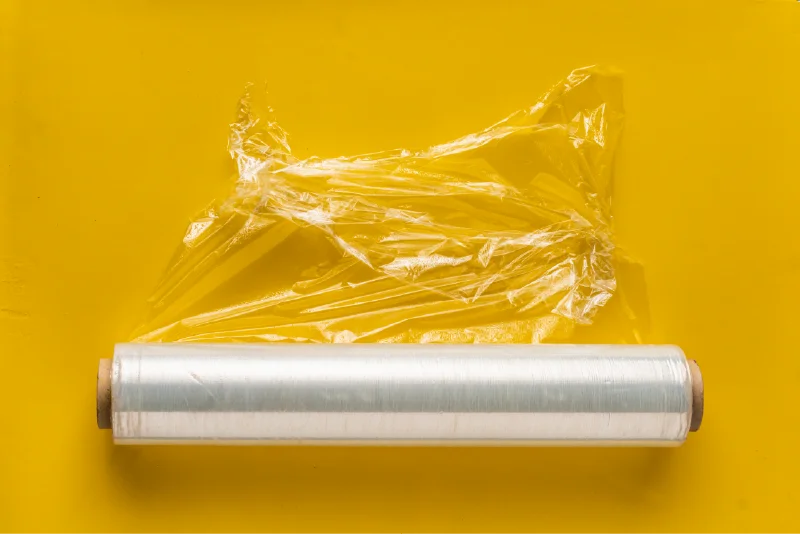
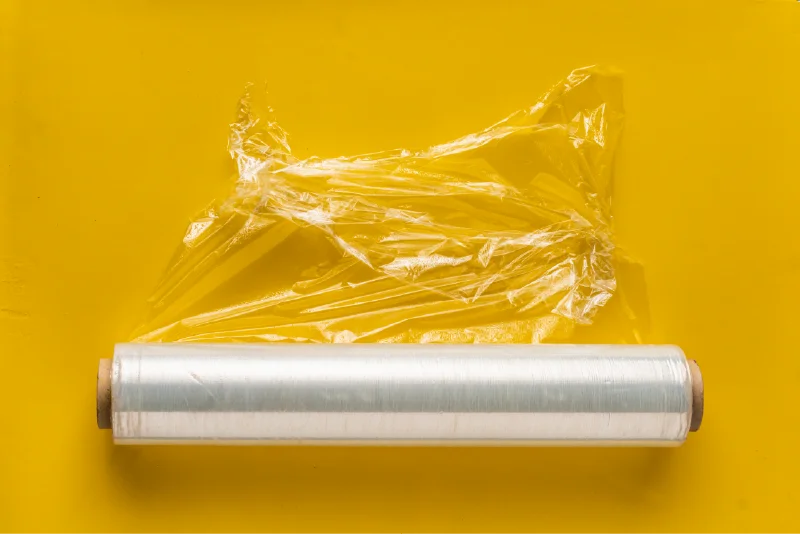
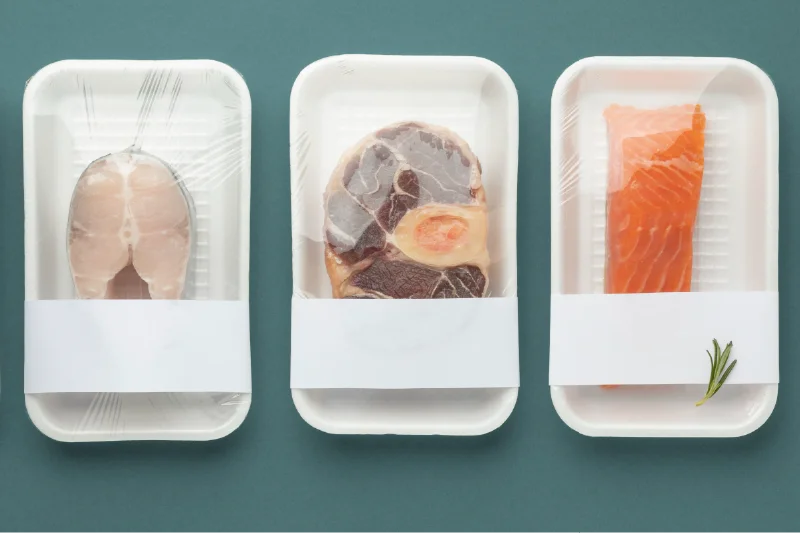
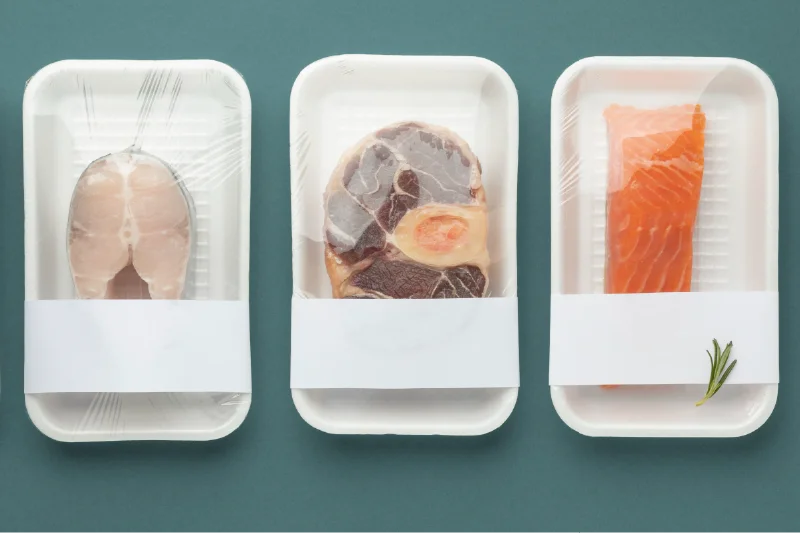
Cellophane is a brittle amorphous material, but the addition of the humectant glycerol gives the film significant flexibility. Regenerated cellulose is a good substitution polymer for synthetic polymers for several use applications since it demonstrates a decently low permeability to water, oil, grease, and air as well as low porosity, thereby showing good exclusion of micro-organisms.
The polymer packaging film is, therefore, useful and popular for primary wrappings for food packaging applications and those of frozen oily foods. Cellophane is fully biodegradable, being broken down by cellulolytic fungi (Fusarium spp., Penicillium spp., and Aspergillus spp.) and bacteria (Clostridium spp., Actinomycetes spp.). However, toxic CS processes are used in most cellophane production and is a worker health concern and reduces the environmental appeal of its substitution for polyolefins. CA is used mostly for photographic film and fabrics but rarely for plastic packaging as it degrades and liberates acetic acid.
Cellulose nitrate or NC was used as part of an early plastic called 'Parkesine' in the 1860s. It has limited use as a principal packaging material but does find use in terms of lacquers. As in the case of many cellulose-based materials, including pure cellulose fiber, its advantage lies in that it is made from straw or wood pulp and, therefore, is an entirely renewable resource as it can be composted or incinerated.
Polymeric Packaging Applications
Polymer packaging materials and other popular materials are both flexible and easily modified but with the advantage of being generated for little cost. Plastics and other polymers occur ubiquitously in food packaging and range from the HDPE milk bottle to PET microwaveable ready-to-eat (RTE) cooked foods trays, cellophane raw-frozen meat wrappings, LDPE salad and confectionary bags, and PS or PP cream or yogurt cartons.
Common uses in a medical context are for medicinal bottles used to carry tablets and capsules or pharmaceutical blister or 'push-through-pack' (PTP) packaging. Pharmaceutical blister packs or blisters make use of a webbing film that can be thermoformed into a mold or die of a specific shape.
Valued characteristics can include gas or water vapor impenetrability, clarity or opacity, low or high melting temperatures, non-toxic components, recyclability, and mechanical robustness. A complex formulation of blends of different types of homopolymer plastics in combination produces copolymers with unique properties.
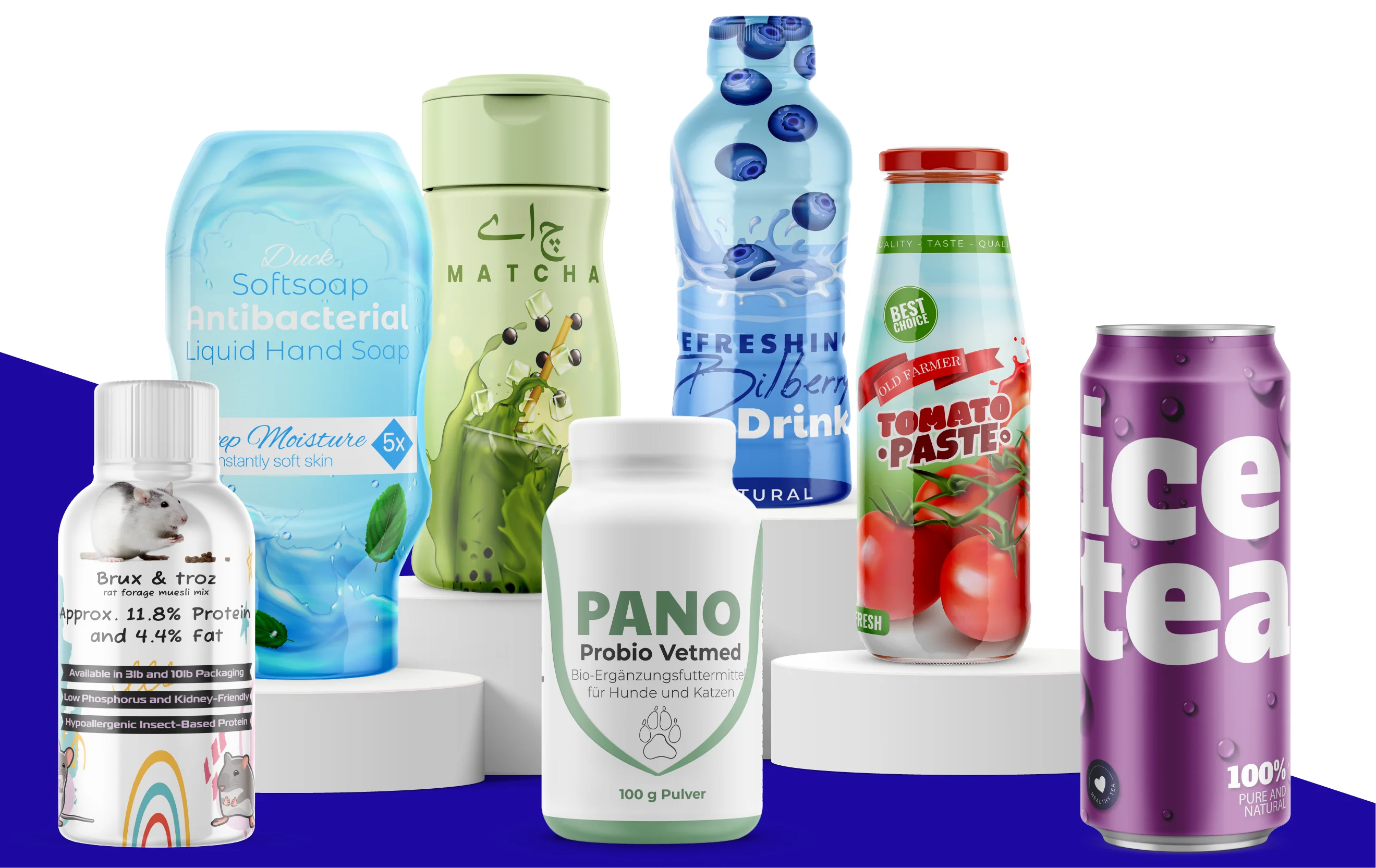
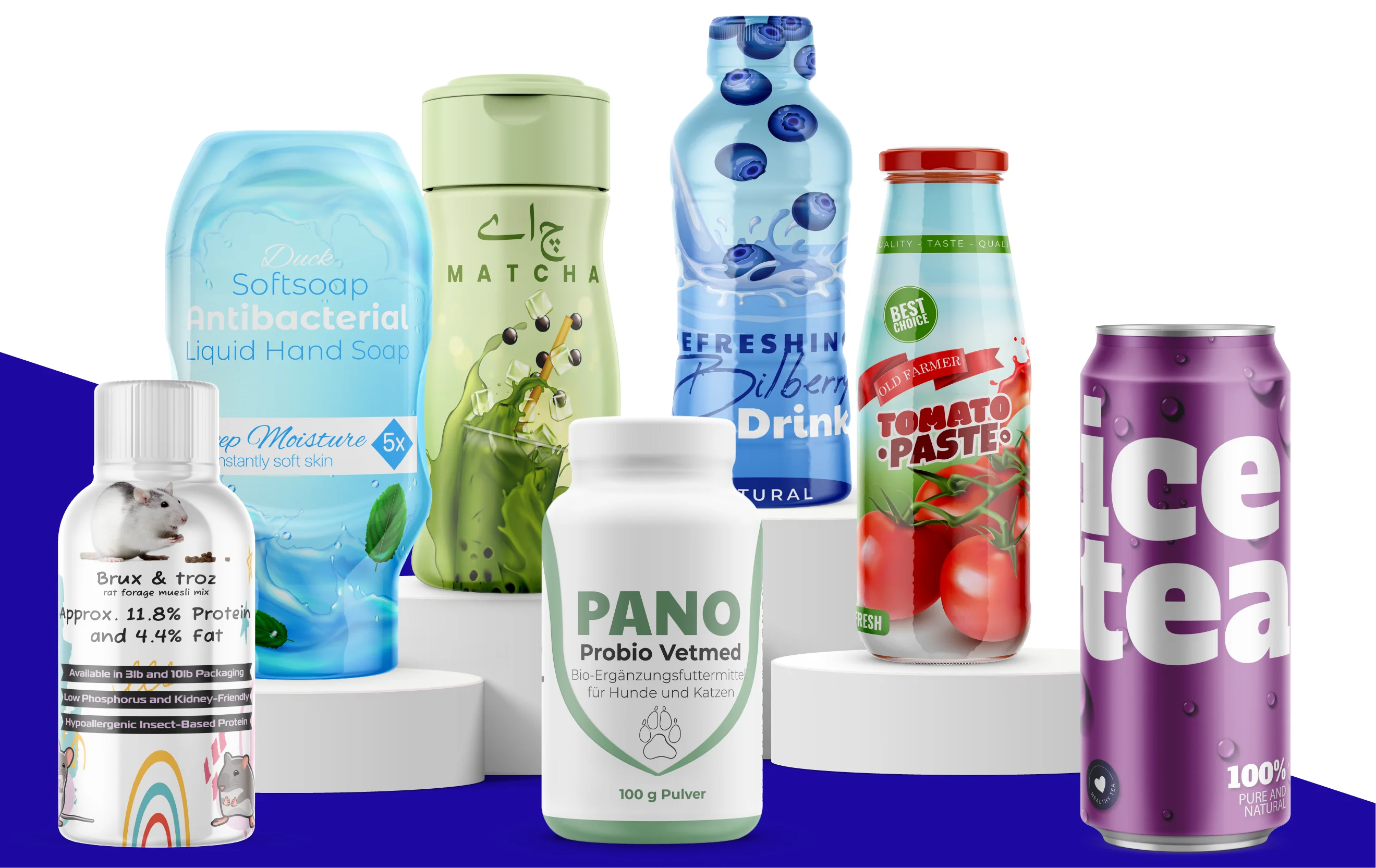
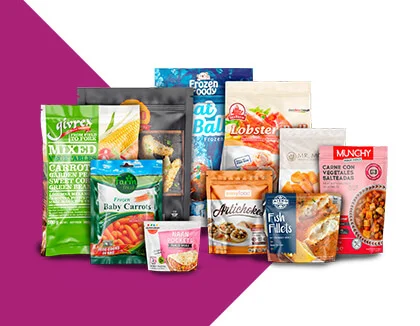
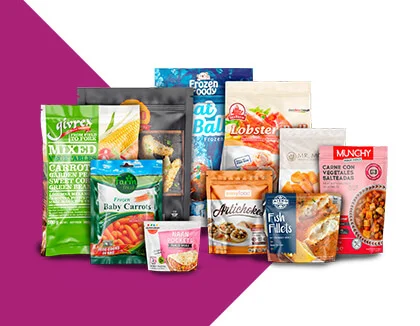
Semi-crystalline vs amorphous polymer packaging
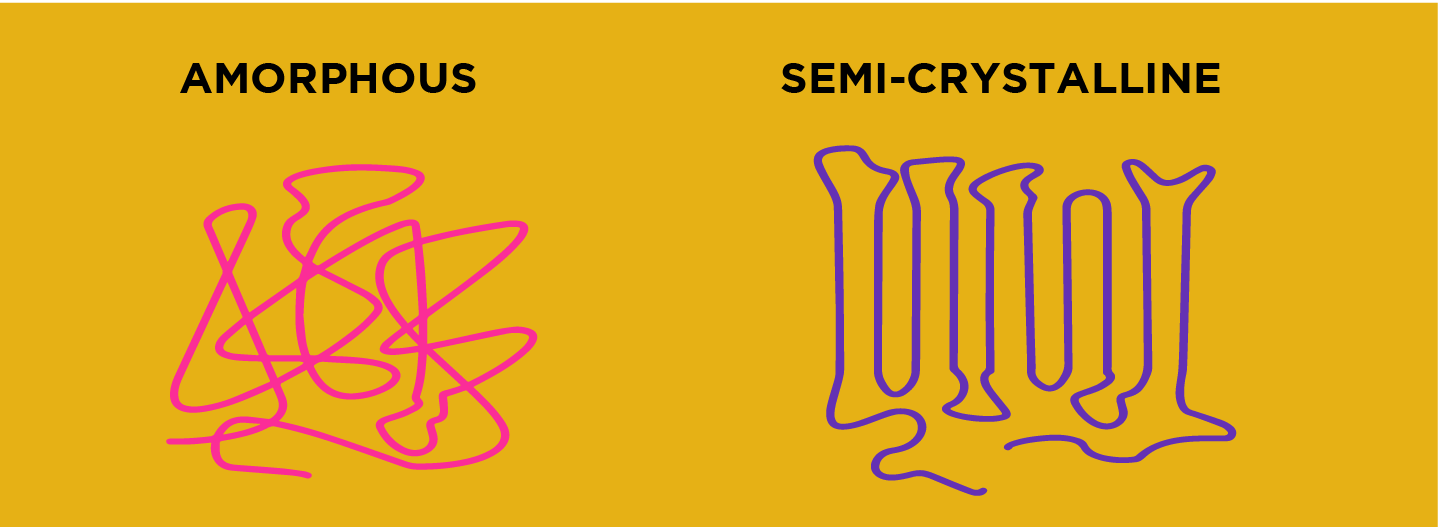
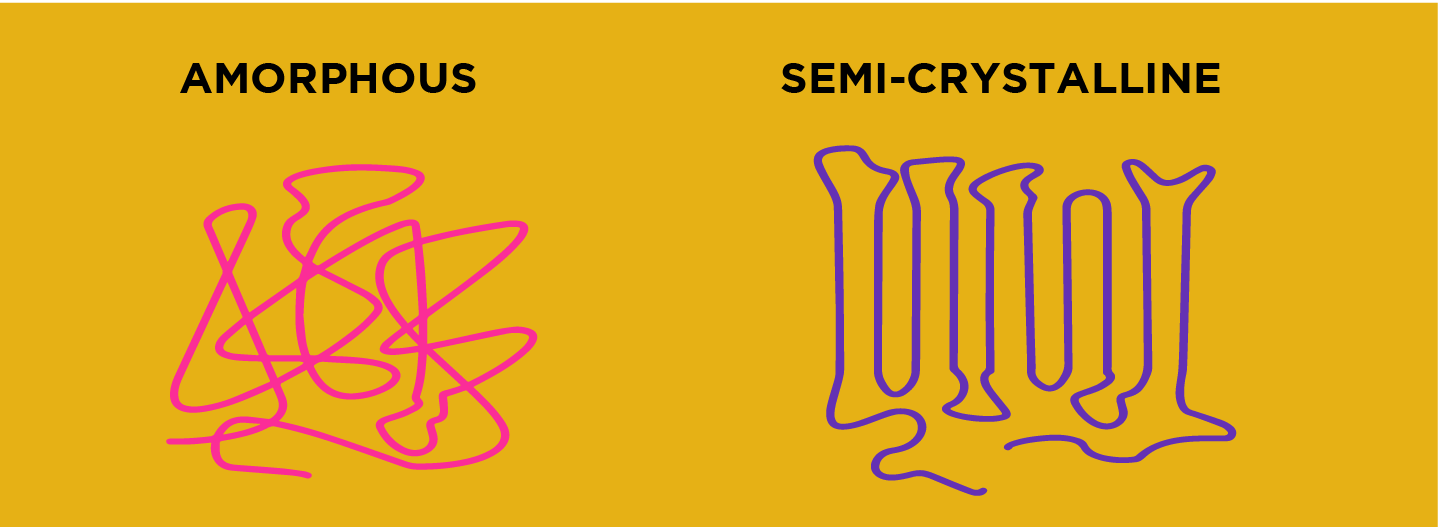
Depending on its molecular structure and functionalization polymers are either semi-crystalline polymers or amorphous polymers. Unlike amorphous-structured solids, semi-crystalline polymer solids demonstrate clear crystallization and melting point transitions. Polymeric materials exhibit a component structure similar to that observed in the supercooled liquid phase but display the typical mechanical properties of a solid.
Amorphous structured syndiotactic and isotactic plastics, on the other hand, exist in a 'metastable state' with respect to any crystalline form.
Polymers used for packaging by percentage
PET | polystyrene | POLYPROPYLENE | LDPE + HDPE | Other Plastics |
---|---|---|---|---|
9% Fill Counter | 11% Fill Counter | 11% Fill Counter | 61% Fill Counter | 8% Fill Counter |
Flexible packaging and bottles | Packing Foam | Trays and lidding | Pouches, bags, and bottles | PTFE, ABS, Nylon PVC |
Polymer Packaging Ingredients
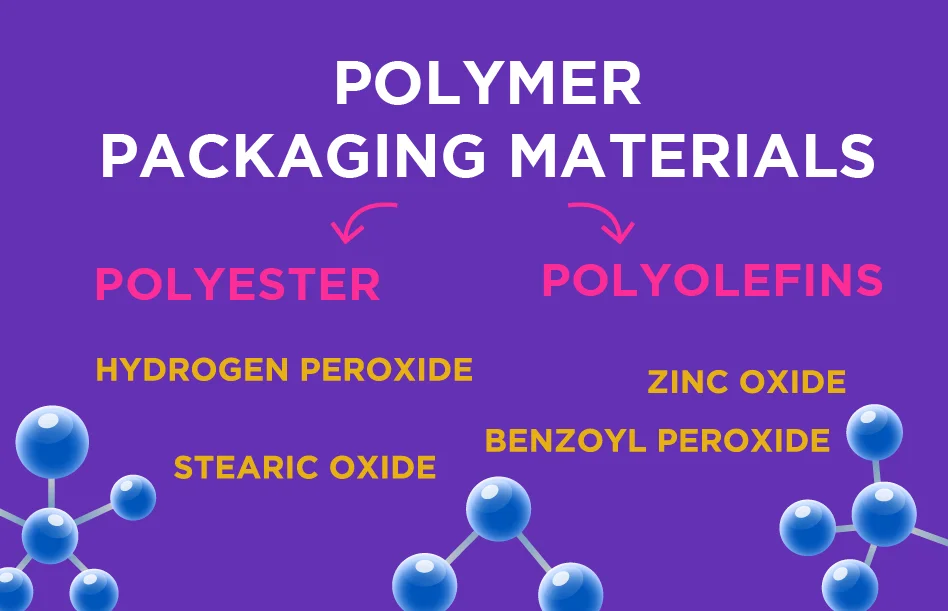
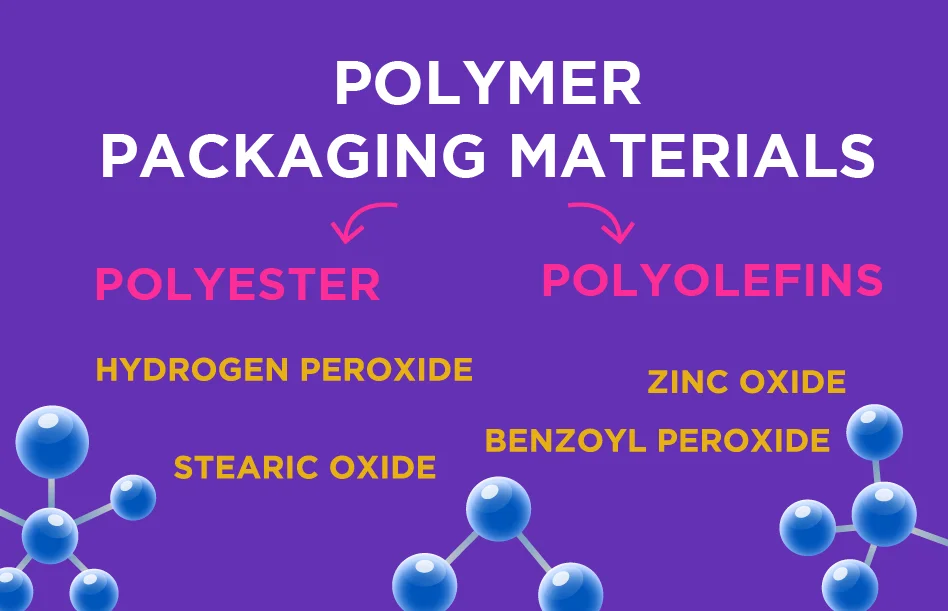
Polymer packaging materials such as polyester and polyolefins routinely include between 10 and 50 ingredients, which are designed to preserve or improve the safety, performance, and longevity or shelf life of the contents. Conventionally, the biggest component in such packaging materials is the polymer packaging itself, with between 1% and 10% of included additives.
Polymerization agents, accelerators, activators, and catalysts such as hydrogen peroxide, benzoyl peroxide, zinc oxide, and stearic oxide are standard monomer function-alisers and cross-linking agents. However, small amounts of unreacted materials might be expected to remain in the plastic, and this has formed the basis of material quality control and choice or selection of the material.
Society is moving towards bioplastics
Recent trends suggest a movement by supermarkets to remove plastic from packaged products in certain jurisdictions with the top five supermarkets working towards replacement of traditional polyolefins with compostable paper or bioplastics fabricated from sustainable sources of starch, corn, or other polylactates in an attempt to further sustainability goals and reduce the amount of single-use plastic packaging. This shows that the packaging market is changing and brands need to prepare to pivot.
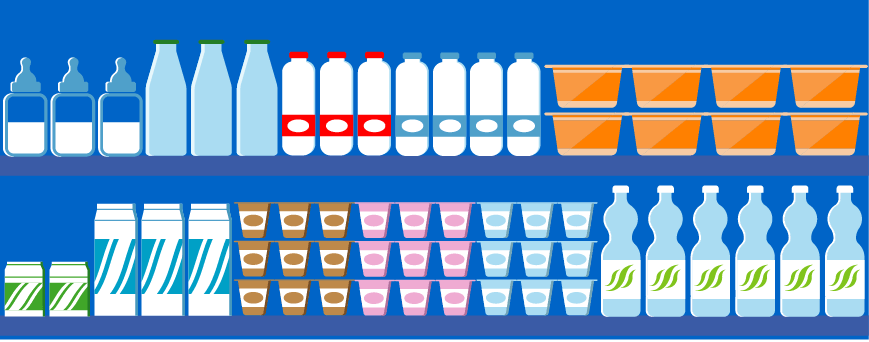
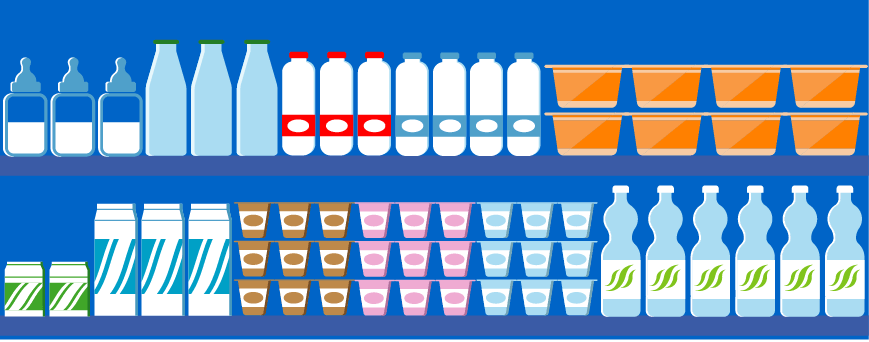
Bioplastics find use as fillers and foams, films, wraps, trays and containers for fruit, egg boxes, meat trays, soft drinks bottles (a recent initiative by Coca-Cola involves monoethylene glycol-PET called PlantBottle), and cartons. Poly(vinyl alcohol), or PVOH (PVA), is a synthetic water-soluble polymer packaging with the general formula [CH CH(OH)]n that has been traditionally used as an emulsifier, adhesive, in paper manufacture as a release lining, as a'textile' sizing agent, as a carbon dioxide barrier in PET carbonated drink bottles packaging, and as a biodegradable plastic sheet for covering sanitary products.
The Environmental Impact of Plastics
Plastics have been 'around' in their present form for 80 years or so up until present times, and are considered, if not recycled, to be an environmental threat thought to be able to persist for 400-1000 years. Since a calculated 6.3-8.3 billion tones have been made to date, with a mere 9% recycled, 12% incinerated, and 79% placed in landfill or accumulated in the environment, this points at very inefficient strategies for coping with such a persistent material
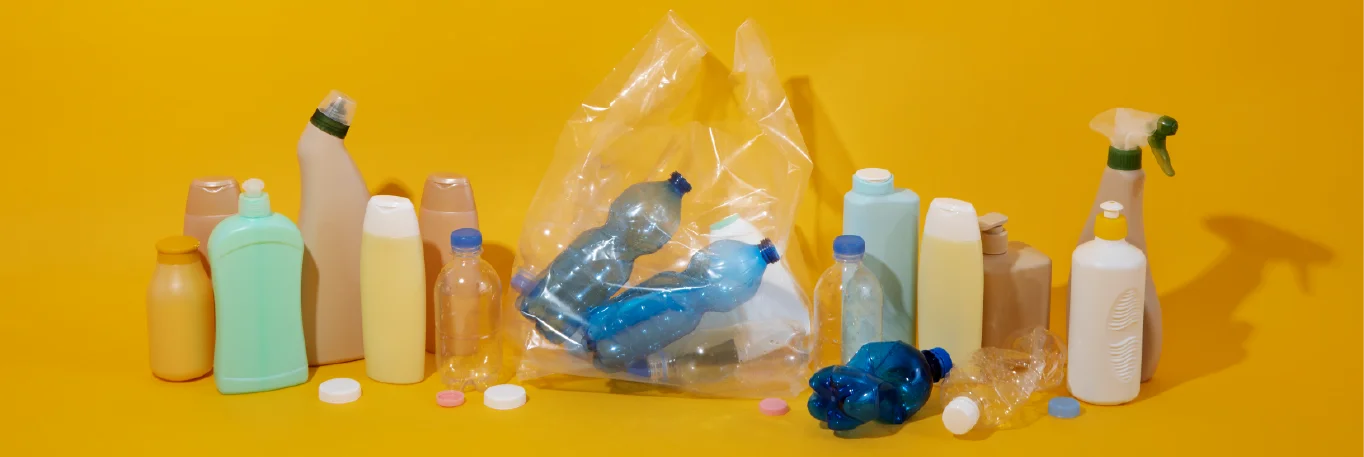
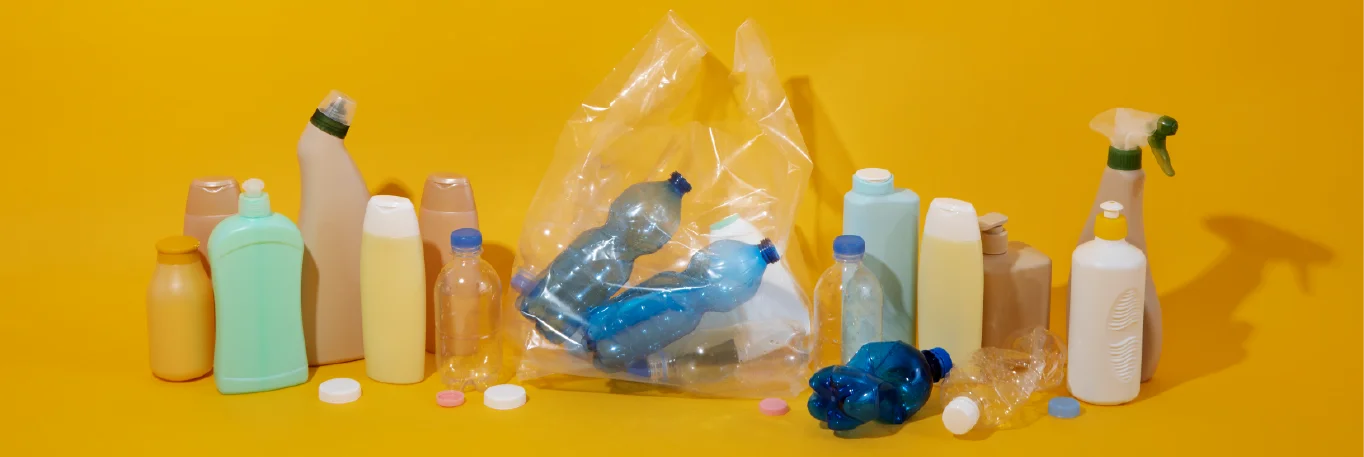
Plastics have been 'around' in their present form for 80 years or so up until present times, and are considered, if not recycled, to be an environmental threat thought to be able to persist for 400-1000 years. Since a calculated 6.3-8.3 billion tones have been made to date, with a mere 9% recycled, 12% incinerated, and 79% placed in landfill or accumulated in the environment, this points at very inefficient strategies for coping with such a persistent material.
In the 45 year period from 1960 to 2005 there was a 1,000% increase in the amount of plastics in municipal waste to the near-present value of 10% by weight (about 40% of plastics are used solely for product packaging). The EU is at present the leading recycling regions at 25-30%. However, many of the G20's most economically powerful 'top table' countries have a poorer record on the recycling front.
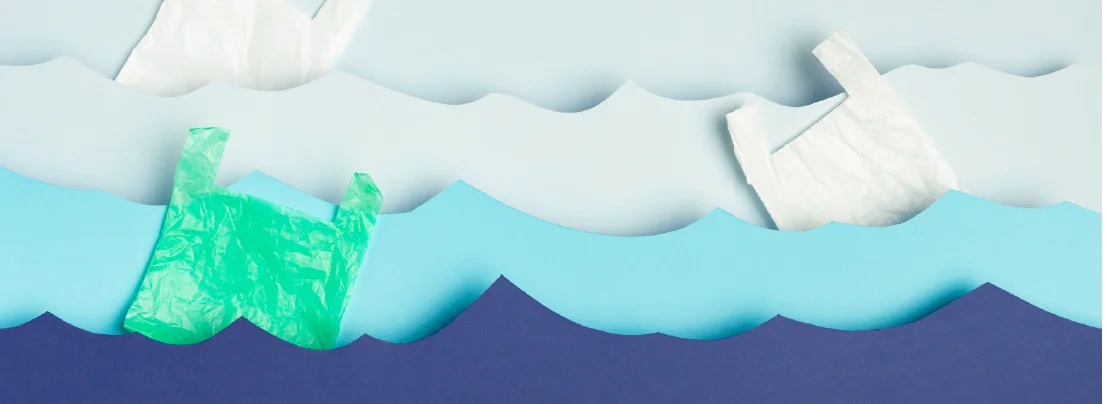
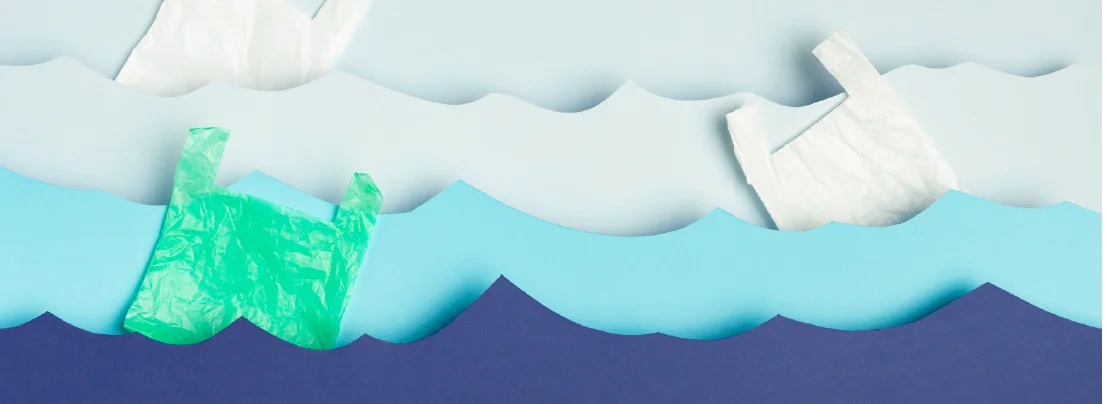
For example, the USA recycles an average of approximately 10% of plastics. Germany recently had the best statistics for recycling, with greater than 60%, and both Turkey and Chile sit at the bottom of the recycling 'league table' with a mere 1-2%. The UK recycled about 37% of its plastics in 2010, some way back from Germany. Notably, Poland has been seen making the most significant improvement of approximately 900% in recycling policy and practice in the last 20 years.
At the current rate of production, as much as 12 billion tons may by 'syphoned off from landfill or generally in the environment by 2050. PE and PET are about the 'best' plastics for consumers in general and routine use as these are the most recycled; however, the usage statistics contradict this notion at present with 36% PE, 21% PP, 12% PVC, and 10% each for PET, PS, and polyurethane (PUR).
Such use means a change in global manufacturing culture is needed as a matter of some urgency as PUR, PVC, and PS represent a major inconvenience since they are not routinely recycled