Consistent Quality Control in Large-Scale Packaging: Why It Matters for Your Business
Introduction to Packaging Quality Control
Manufacturers and businesses have a responsibility to meet customer satisfaction with their finished product, and this applies to both the product itself and the packaging quality standards. After all, what's the point of manufacturing and shipping a high-quality product if it arrives to your customer broken because the packaging materials and product packaging were low-quality? Would your customer really order anything from you ever again after experiencing such extreme quality issues? Probably not.
In this blog, we'll discuss why quality control is important in large-scale packaging in various industries, and how a packaging quality control checklist can help catch packaging issues before they become a massive problem for businesses. Read on to learn more about how manufacturers can maintain high standards with their packaging.
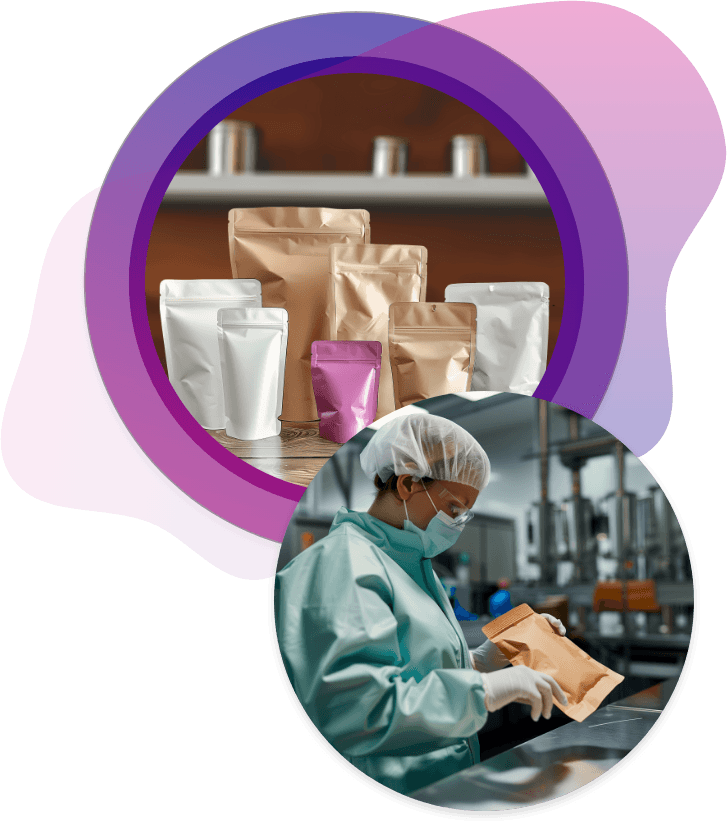
Why Quality Control is Critical in Large-Scale Packaging
As mentioned above, quality control in packaging is critical in large-scale packaging because the package (and its quality and defects) is often the first thing a customer sees. It plays a crucial role in the brand perception of your company. Not only is high quality packaging essential to wow your customers with beautiful and attractive product packaging, but the packaging itself needs to stand up to rough handling so the product arrives intact and functional. It also needs to meet regulatory compliance standards and prevent contamination.
Here are a reasons why packaging quality control (and establishing a reliable packaging quality control checklist) is essential to maintaining the quality standards of your product.
Quality Packaging Minimizes Product Loss
Low quality product packaging or food packaging that breaks or spoils the product inside can cost you a lot of money. Not only will you have to replace the product but, without a good quality control process in place, you won't be able to catch inefficiencies or mistakes in your packaging line.
Helps Avoid Fees from Mistakes
From surcharges imposed by logistics partners for improper labeling to fines or fees from ports or third-party logistics providers due to messes caused by improper packaging, improving your packaging quality control can help you avoid costly and ongoing fees from these oversights. It can also improve quality assurance.
Improves Your Workflow
Another crucial aspect of quality control checks for packaging, specifically, is that you can catch small issues before they become catastrophic issues. By continually monitoring your packaging quality control processes and making improvements, you can improve your day-to-day workflow and avoid costly product safety issues caused by product recalls due to poor quality control in packaging.
Improves Your Reputation
This is a big one. If your company is constantly dealing with customer complaints about product quality due to inefficient product packaging, this can have a huge impact on your company's reputation. An unhappy customer is often more vocal than a happy one, so catching packaging mistakes before they become major issues can help you maintain consistency and meet customer expectations.
Helps Meet Regulatory Standards
From temperature-controlled packaging for frozen goods to breathable packaging for fruits and veggies, there are plenty of standards and requirements that the packaging industry needs to meet. By including these as a checkpoint in your packaging quality control checklist, you can make sure your packaging is of the highest quality and meets all safety regulations.
Creates a Better Supply Chain
Beyond customer satisfaction and cost, improper packaging can impact the entire supply chain: including your own employees. Improper packaging can lead to injuries at the workplace from pallets falling over or items leaking due to product damage and causing slips and falls. It can also improve the environmental impact of your products, as it will cut back on the wasting of consumer products.
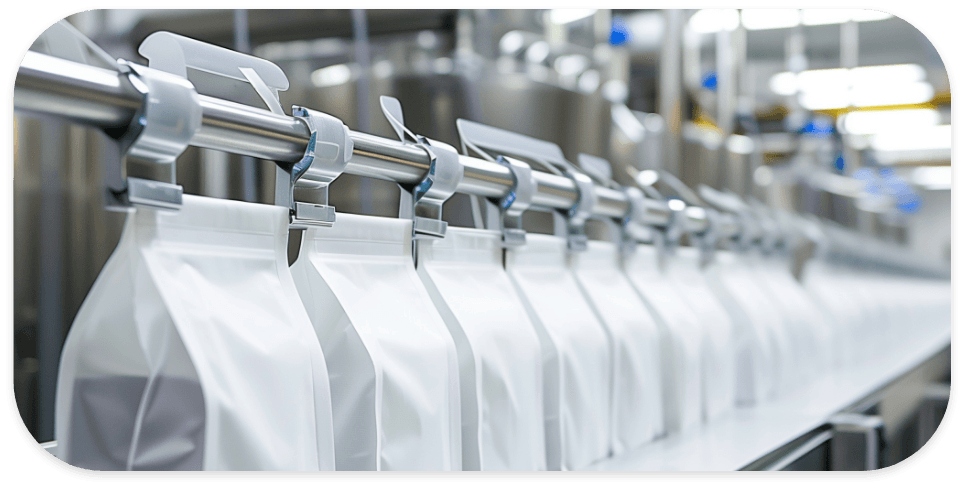
Key Elements of a Quality Control System for B2B Packaging
If you're putting together your first packaging inspection checklist, there are a few things to keep in mind for B2B packaging. Depending on your specific industry or company and what type of raw materials you package, you may want to include other checkpoints in your production and shipment checklist.
Inspection of Incoming Packaging Materials
Ensuring that the raw materials used in packaging meet required safety standards before production begins helps prevent defects and ensures that the final product meets packaging quality expectations. You'll want to make sure the materials meet established standards outlined on the purchase order, and provide your team with the proper training so they can perform these inspection procedures on their own so you can save time.
Monitoring of the Packaging Process
Effective monitoring helps detect issues early, reduces waste, ensures compliance with necessary standards, and optimizes the production process, from production all the way through shipment. This includes real-time process monitoring, quality control checks during packaging, audits of your packaging line, a post-packaging inspection, and establishing a feedback loop for continuous improvement of your packaging process.
Testing for Durability and Compliance
This is where the packaging quality control process gets a little bit fun! You'll need to perform in-depth quality control testing to understand if your packaging truly helps prevent product damage. Some tests to consider include a drop test, compression test, vibration test, an impact test and, of course, regulatory compliance testing. You'll need to look at all the various aspects of your packaging to truly make informed decisions about its quality.
Standardization Across Batches
To truly be able to say that you have high quality packaging that meets customers expectations and doesn't damage your brand reputation, your production packaging should be consistent across the board. You'll need to use special technology to test for standardization across batches, and leverage essential tools like dielines, templates, and automated systems to ensure quality and consistency.
Common Quality Control Challenges in Warehouses
Proper packaging quality control comes with a host of challenges, including managing large inventories without errors, balancing speed with accuracy in the packaging process, and ensuring compliance with industry-specific regulations, such as those set forth for the food, pharmaceuticals, and health and wellness industries. Fortunately, an effective packaging quality control checklist can help you maintain quality standards throughout the production process, ultimately resulting in high quality packaging that will help you maintain product quality and packaging integrity.
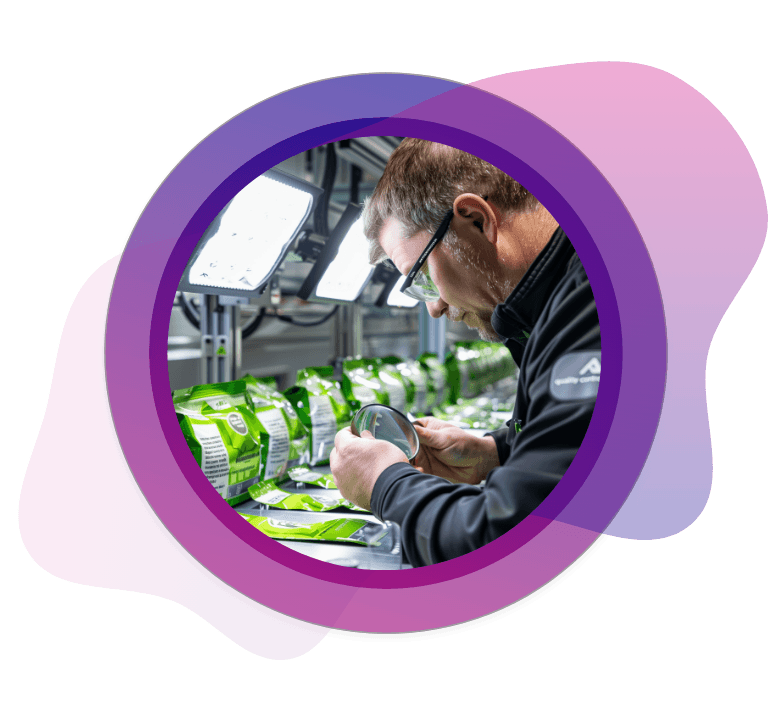
How CarePac Supports Consistent Quality Control
ISO 9001:2015 Certification: A Commitment to Quality
At CarePac, we are proud to adhere to ISO 9001:2015 certification, a globally recognized standard that ensures our quality management system is structured for consistency, reliability, and continuous improvement. This certification establishes rigorous criteria for our packaging processes, helping us:
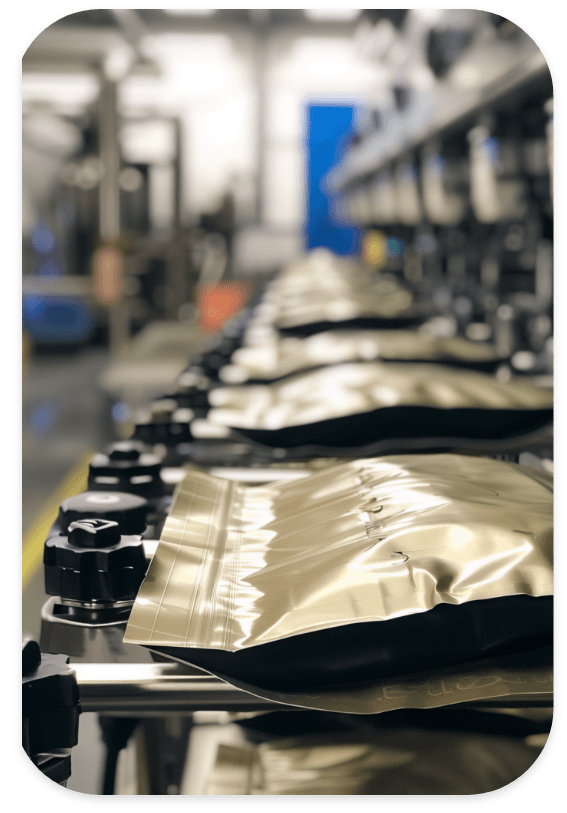
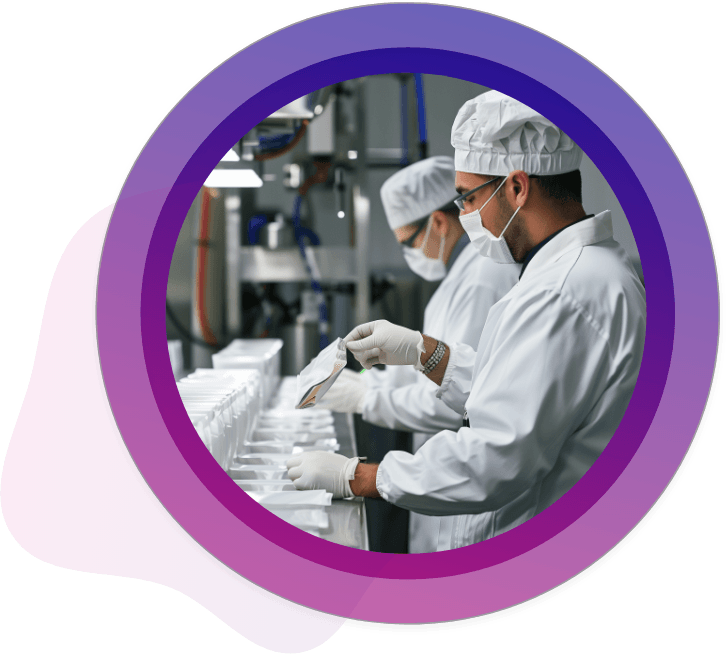
By implementing ISO 9001:2015 standards, we reinforce our commitment to excellence, guaranteeing that our clients receive packaging solutions that meet and exceed industry benchmarks.
Our custom packaging solutions are designed for large-scale operations, and we have our own internal packaging quality control checklist that we leverage. This ensures that our packaging meets your expectations and that you'll be pleased with the finished product. We work with manufacturers of all sizes to create high quality packaging, and can work with you to create your own quality control checklist as it relates to your product packaging.
Don't leave the safety and quality of your food to chance. Contact us today to find the right packaging solutions that will keep your business compliant and customers safe.
Let's Get Started
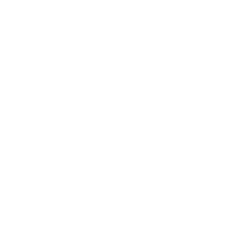
Made In
The USA
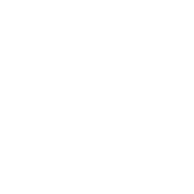
Full Pouch
Customization
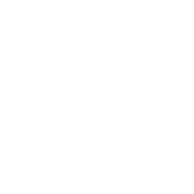